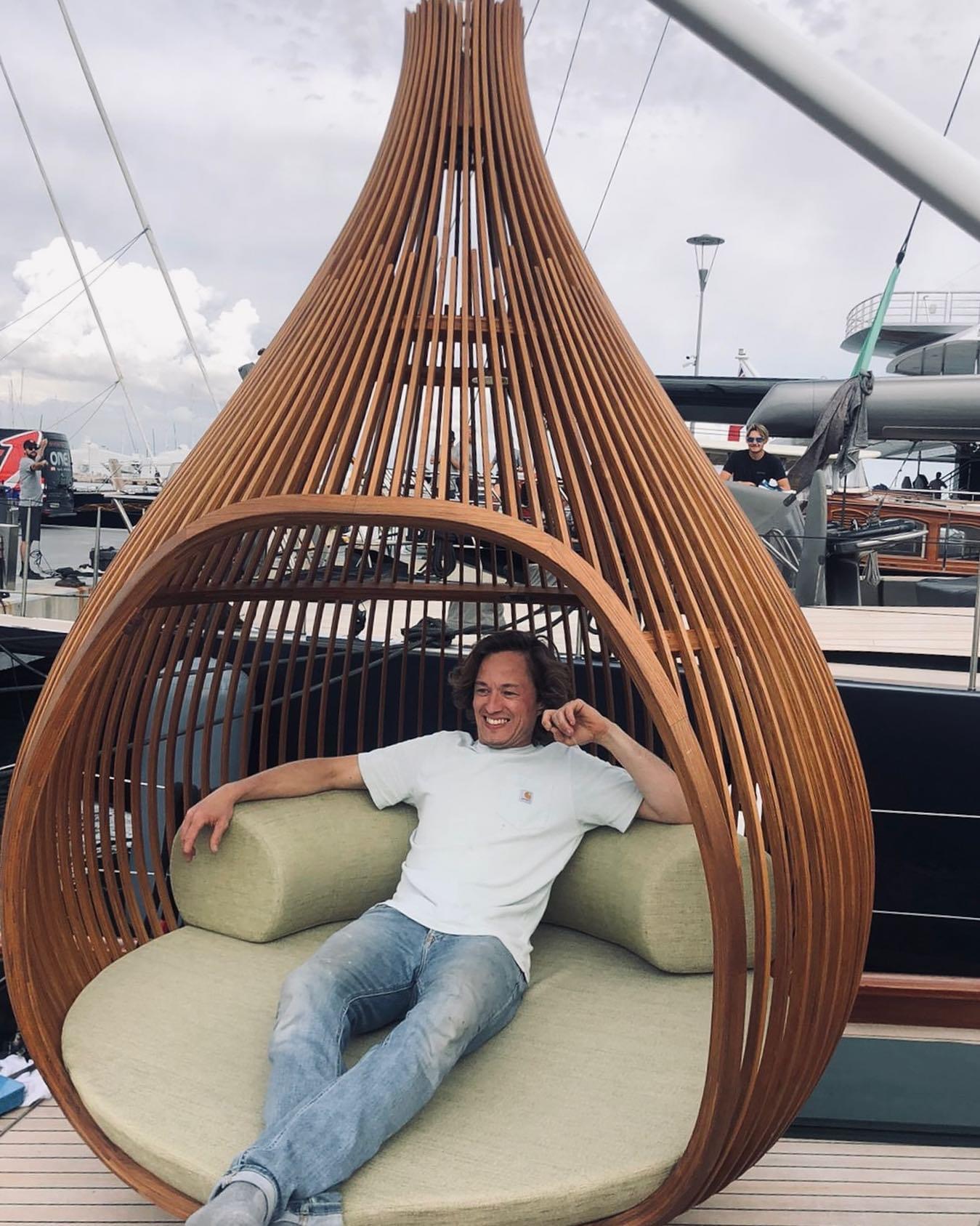
Fauteuil suspendu Teardrop
Robert pensait que la conception de cette chaise serait impossible. Découvrez comment il y est parvenu.
Shape Yacht Joinery
Yacht building and joinery
Custom wooden furniture

How Cutr helped create the Teardrop
The Cutr team were on it the entire time, super happy to help, and responsive.
The finished product that arrived was perfect
Cutr understood the creative route I was trying to go down. They spoke my language.
Teardrop Chair
The unique Teardrop chair was brought to life by Robert Coleby, a craftsman with a passion for cabinet and furniture making and a wealth of experience in boat building at Spirit Yachts. When presented with the opportunity to work on a hanging chair design for a yacht, Robert seized the chance to showcase his skills and creativity.
Robert considers himself a versatile designer and cabinet maker who specialises in solving complex design problems to create unique and innovative products.
Robert Coleby
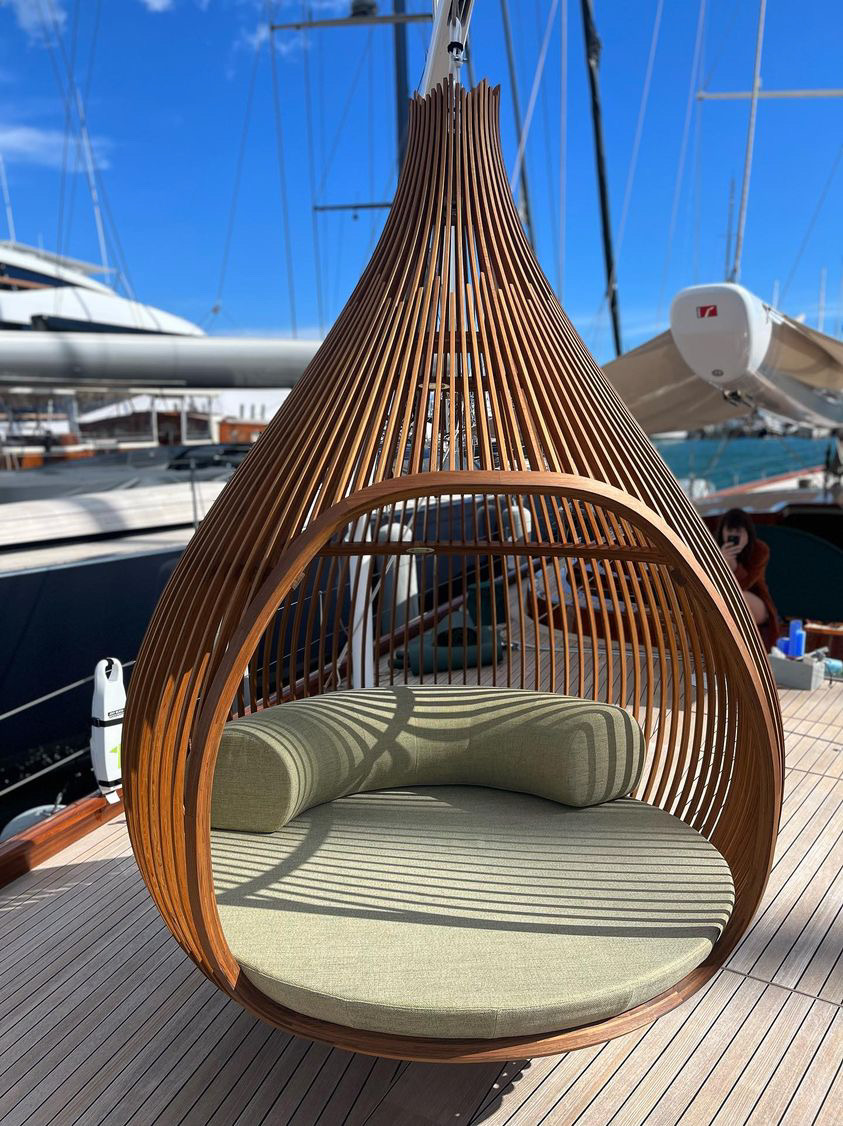
Where did the idea of the chair come from?
Inspiration Behind the Chair
The concept for the chair was born from the yacht's interior, which embraces smooth, organic shapes and avoids any square or upright elements below deck. Keeping this distinctive aesthetic in mind, the client shared a concept sketch that immediately caught Robert's attention.
"While the design looked fantastic, I realised some major adjustments were necessary to ensure the chair's functionality on a moving yacht. It needed to rotate and move freely in all directions to withstand the pressures from any waves and motion".
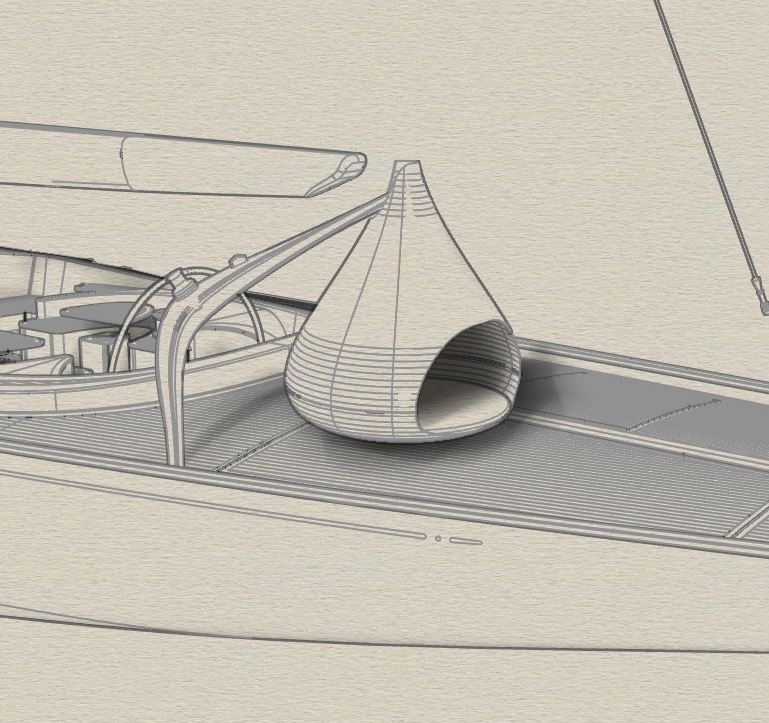
"The chair had to be designed to break down into sections for easy storage in the yacht's lazarette during sailing".
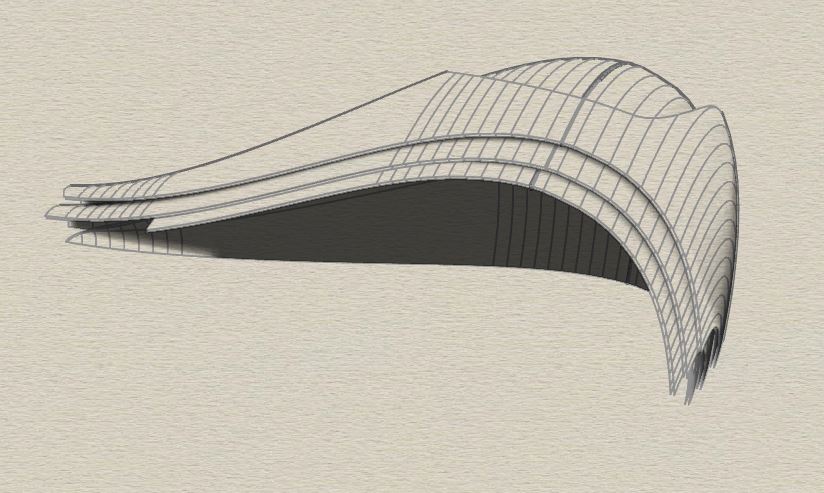
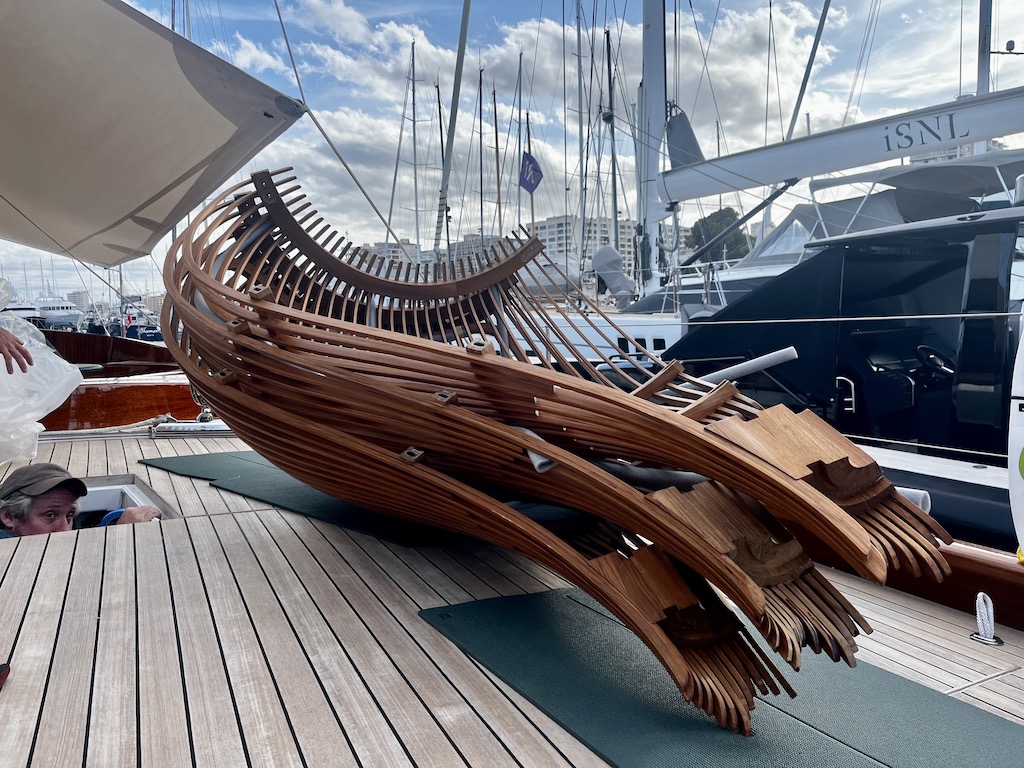
What did you do next?
"We set about looking at proportions. Making 2D life size cardboard cutouts we began to get an idea of the shape and how it looked onboard".
The Design Journey
The design process began by exploring the chair's proportions. Using life-sized cardboard cutouts, Robert and his team could visualise how the chair would look and fit onboard. They quickly realised that the existing davit didn't provide enough height from the deck. To address this, they opted for a longer carbon davit, allowing them to achieve the desired chair size while ensuring sufficient clearance.
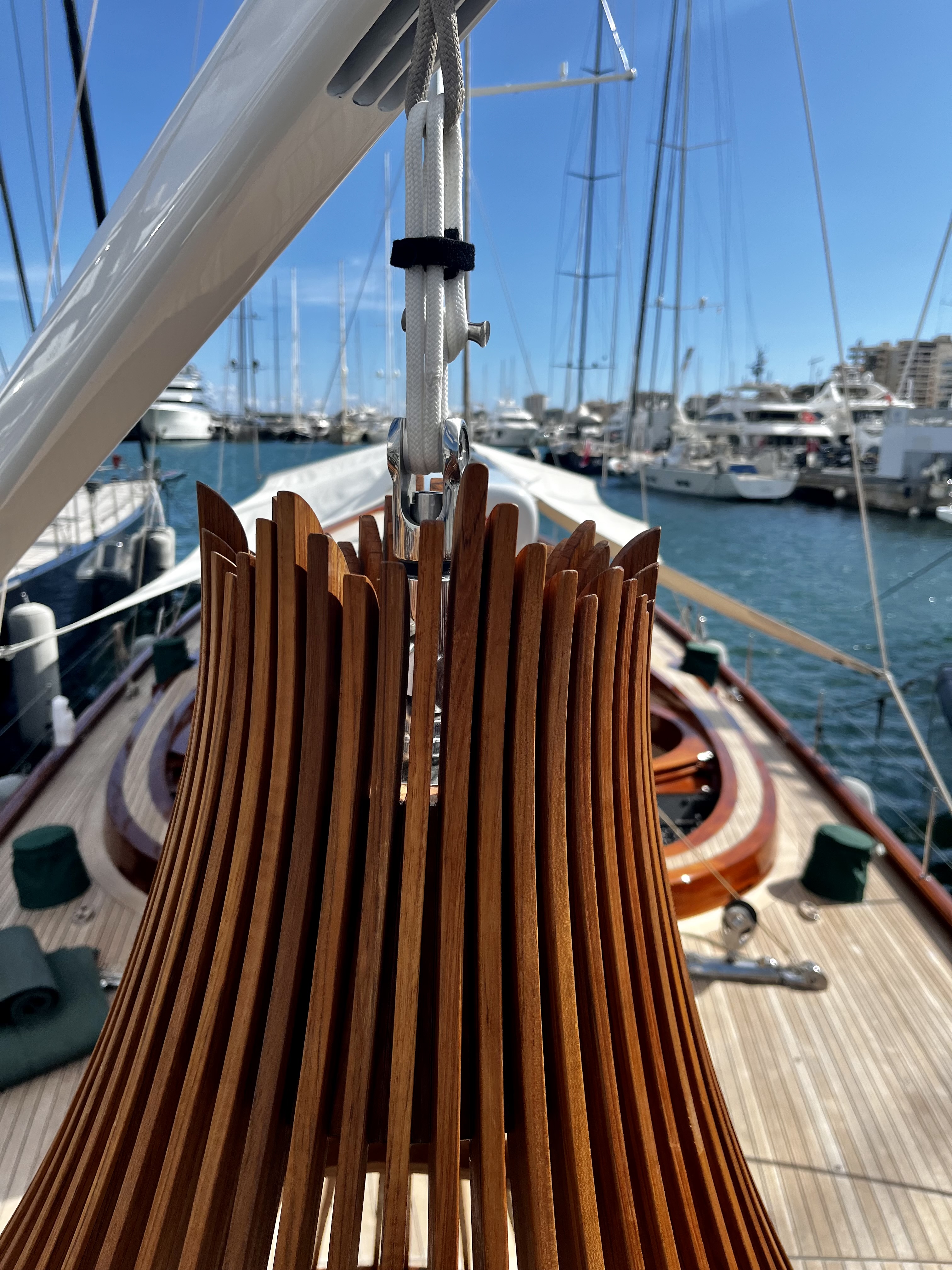
Robert collaborated with naval architect Neal Pawson, leveraging his expertise in CAD to transform two-dimensional plans into a detailed three-dimensional model. Together, they refined the dimensions and curves of the chair's opening hoop, striking a balance between practicality and aesthetics.
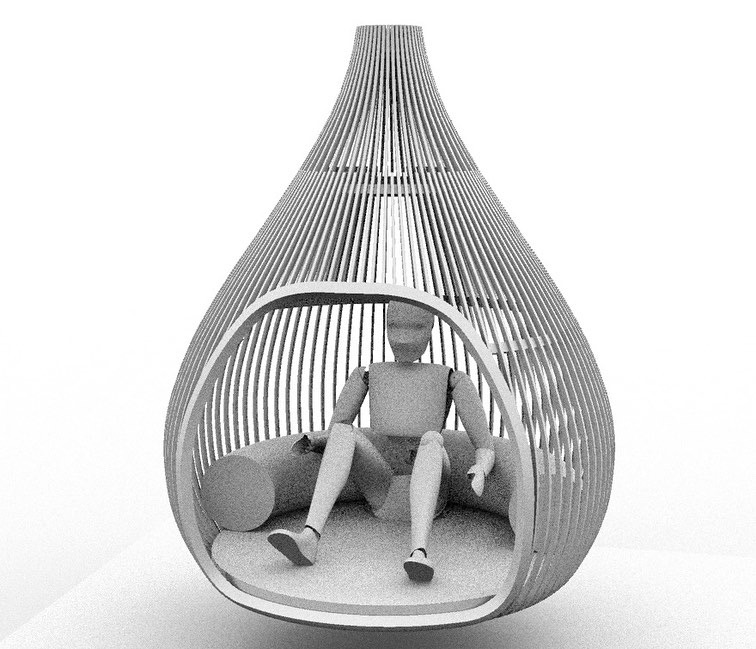
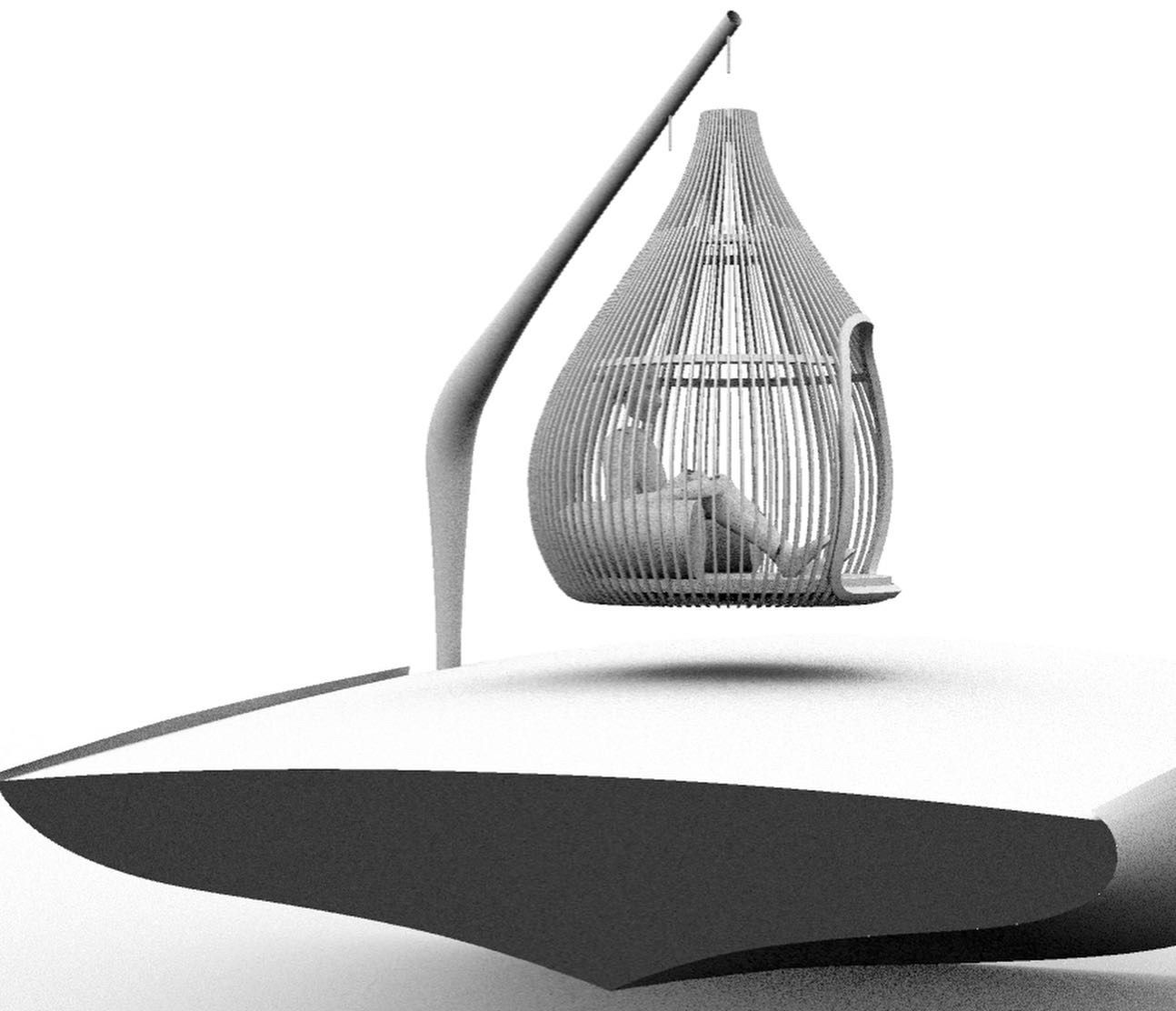
Was it smooth sailing from there?
Not at all! The manufacturing phase encountered some hurdles along the way. The complex mould required for the opening hoop necessitated a specialised 5-axis CNC machine, which was challenging to find locally. Thankfully, Robert received a recommendation to connect with Cutr, who swiftly helped him find a suitable production partner.
"Although there was a brief setback when the operator of the first production partner's machine quit, Cutr quickly found the production partner Kleizen, ensuring the project's continuity".
The manufacturing process took time due to the initial design's complexity, requiring intricate machining angles and specialised cutters. However, after simplifying the design, the production progressed smoothly. The final mould arrived and assembled perfectly and was ready to go. However, constructing the chair's opening was complex and time-consuming.
"Each hoop is made from seven layers of teak. We're only able to glue one layer at a time to ensure that all the joints are tight and the timber adopts the correct shape on the mould".
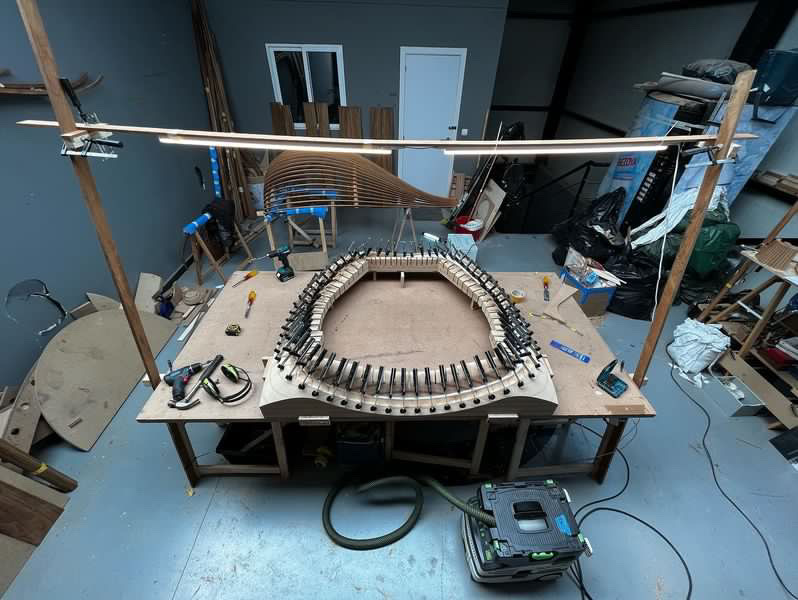
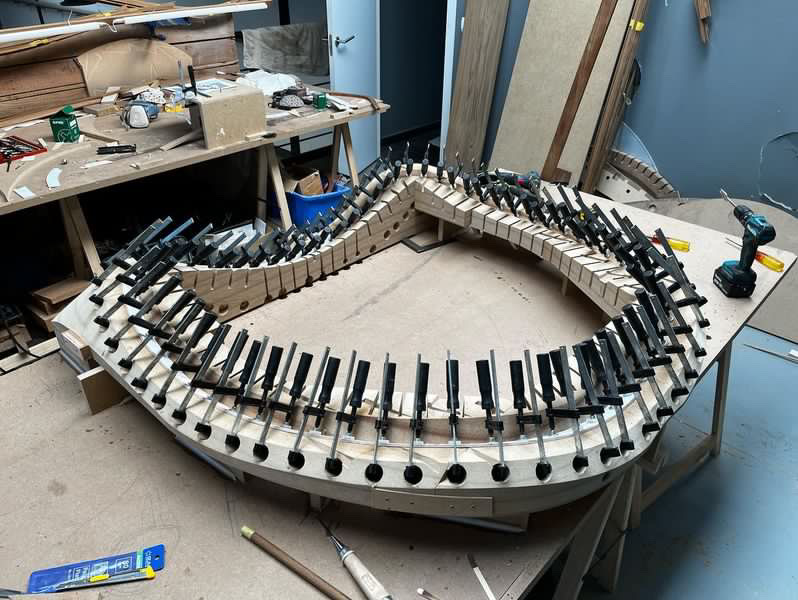

"The 96 battens that formed the chair's vertical pieces were meticulously crafted by laminating teak strips together and skilfully clamping them onto moulds. A joint exists at each intersection of a batten and a hoop, totalling nearly 340 joints".
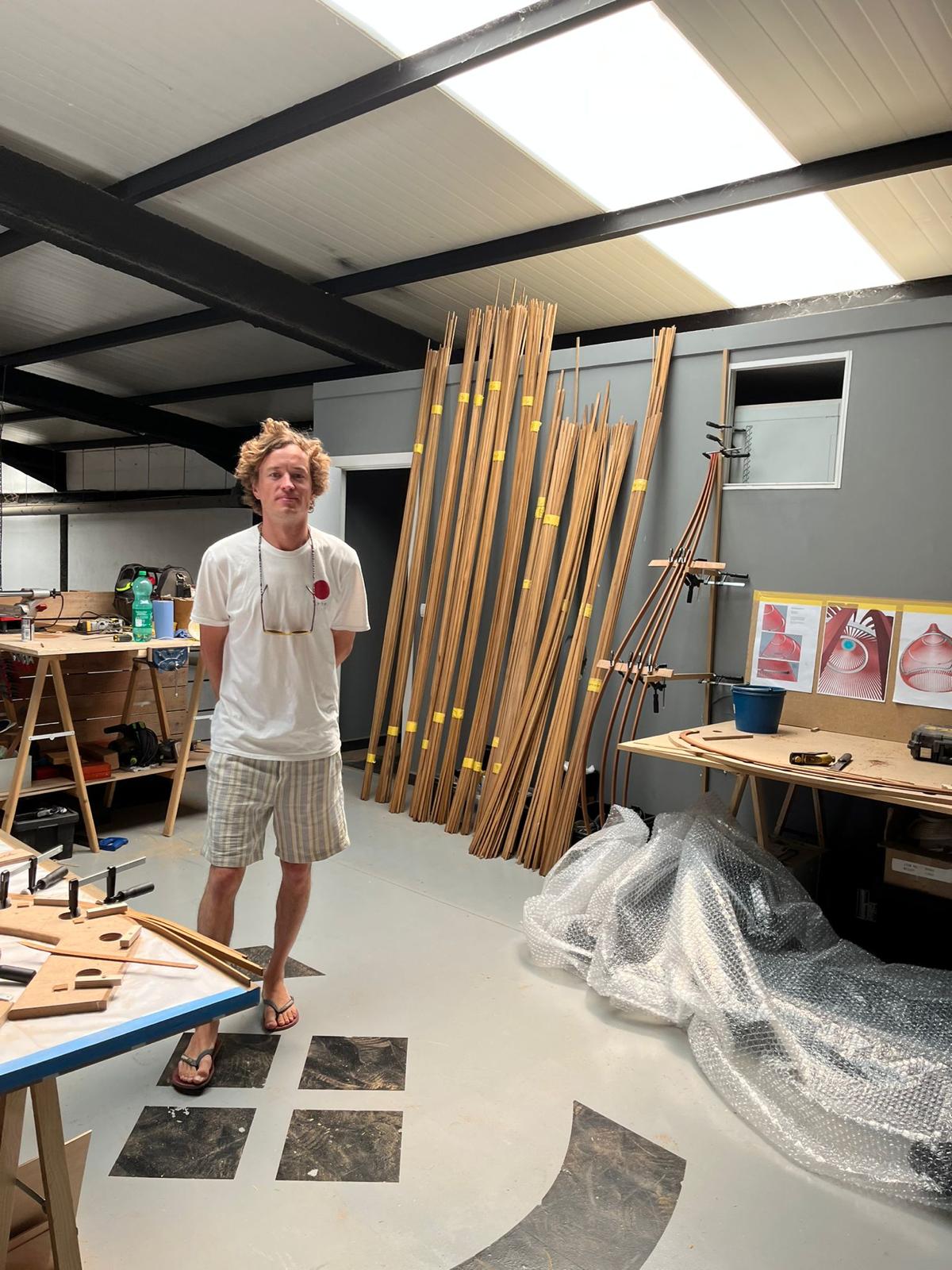
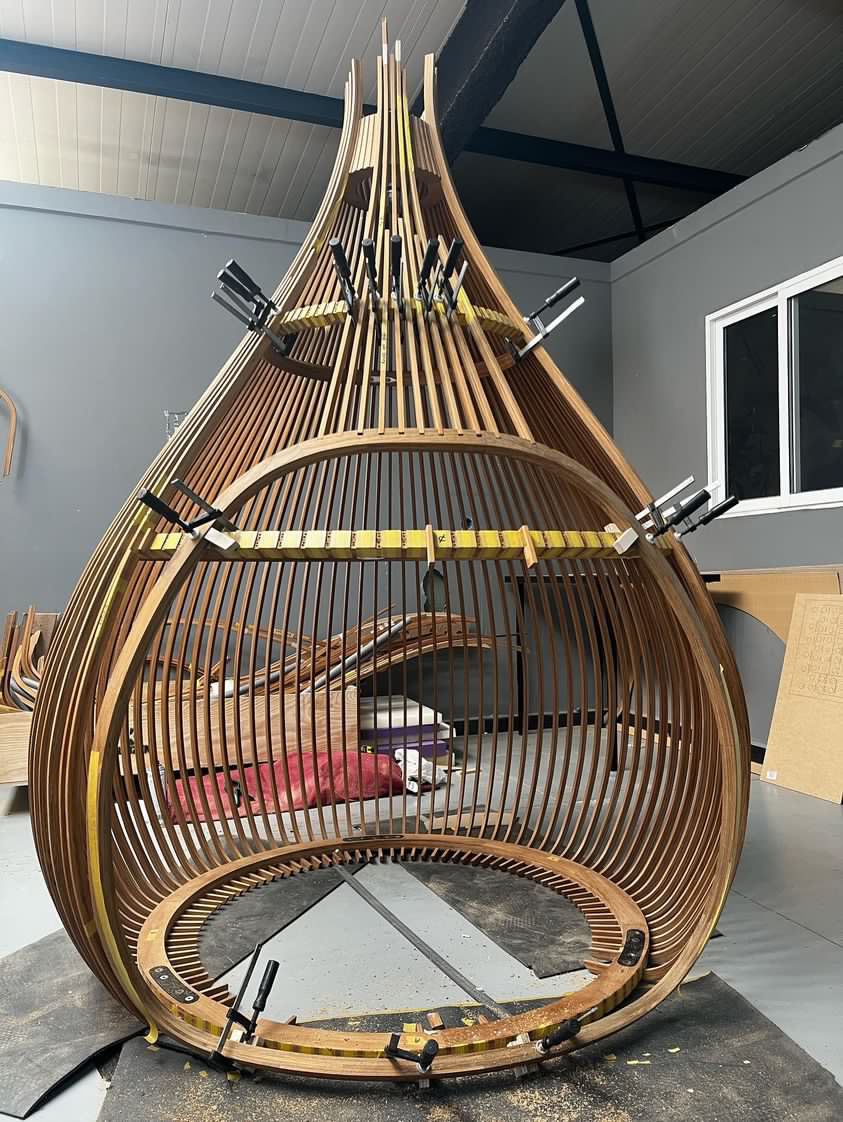
Making Progress
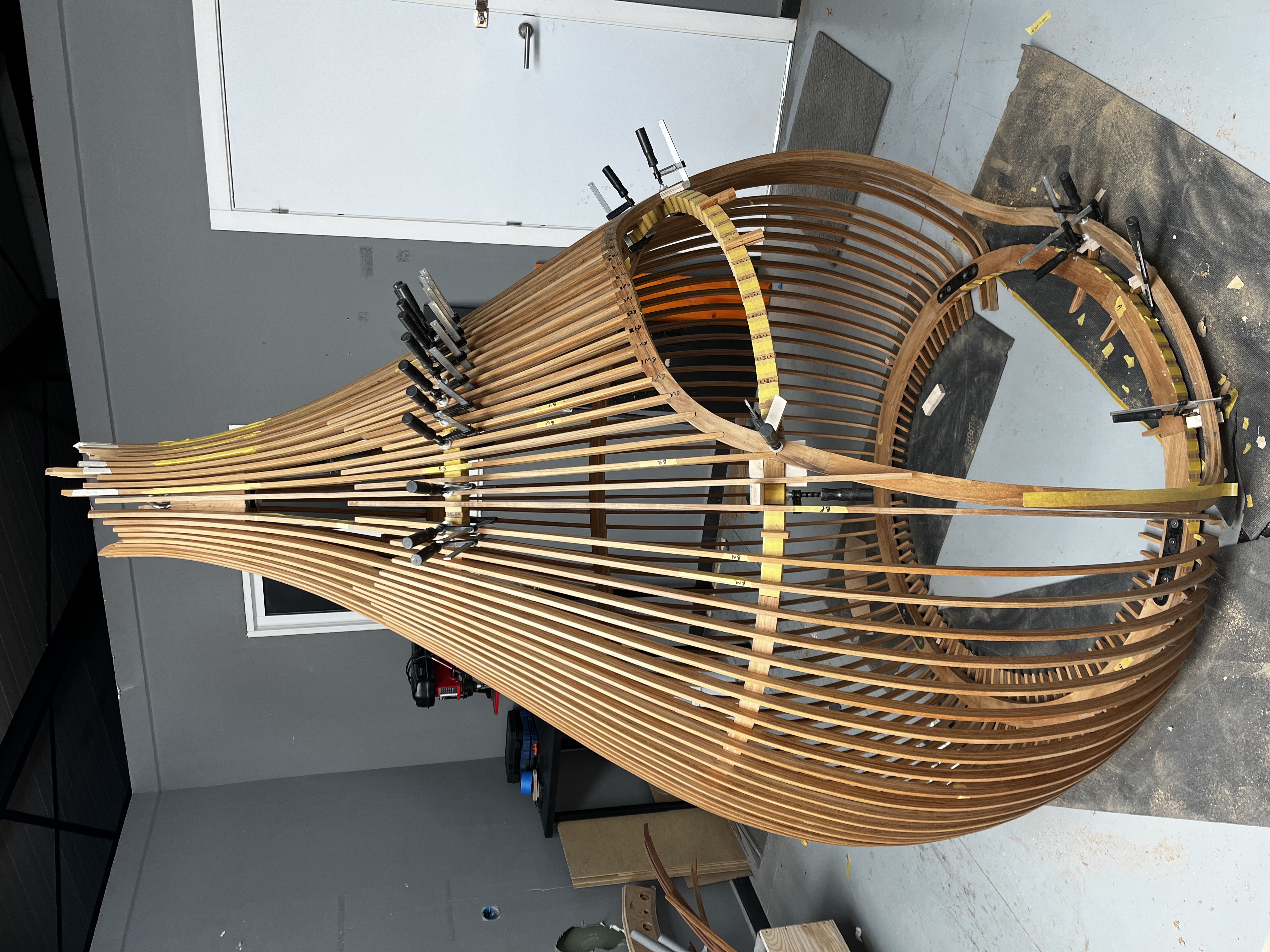
The finished product
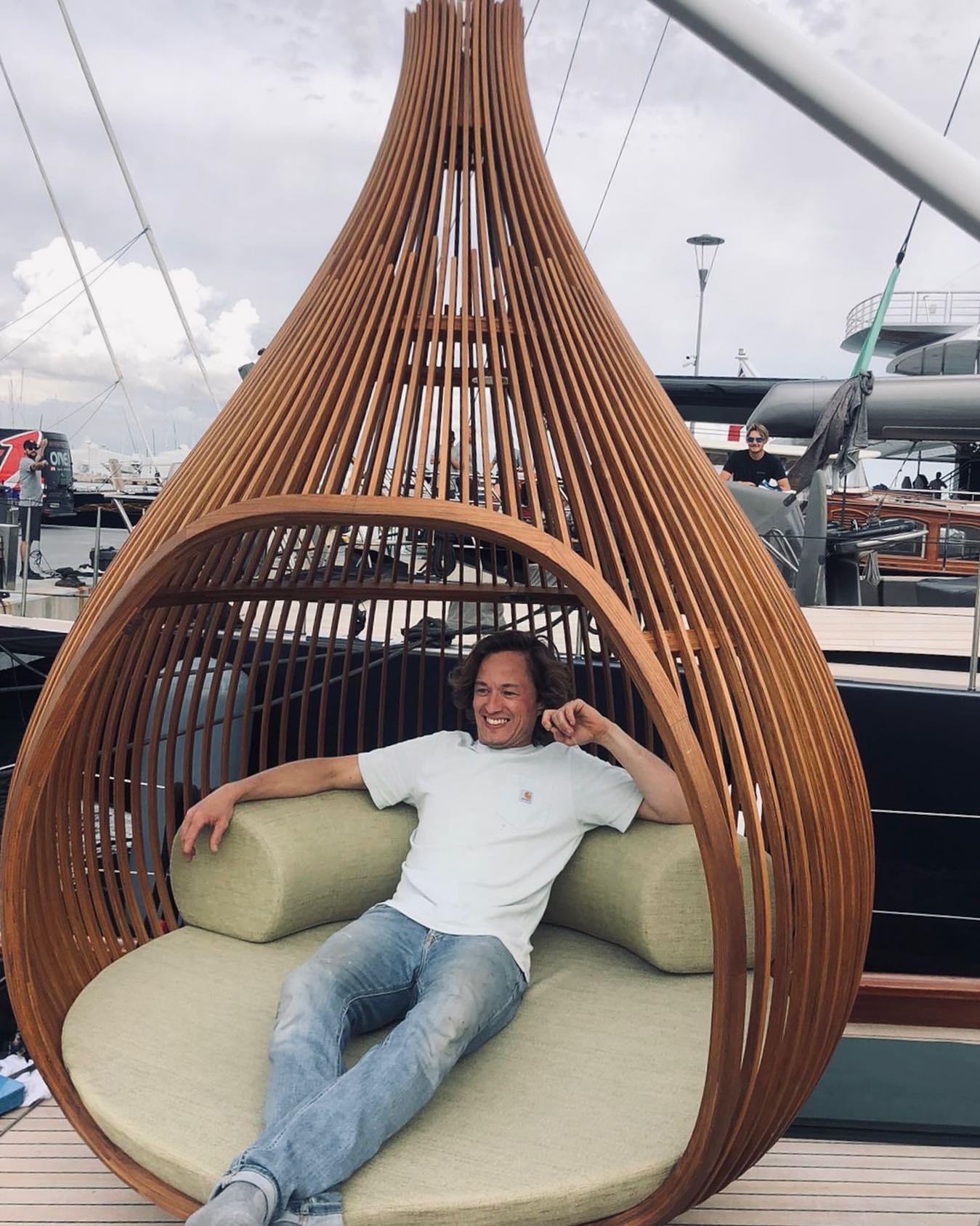
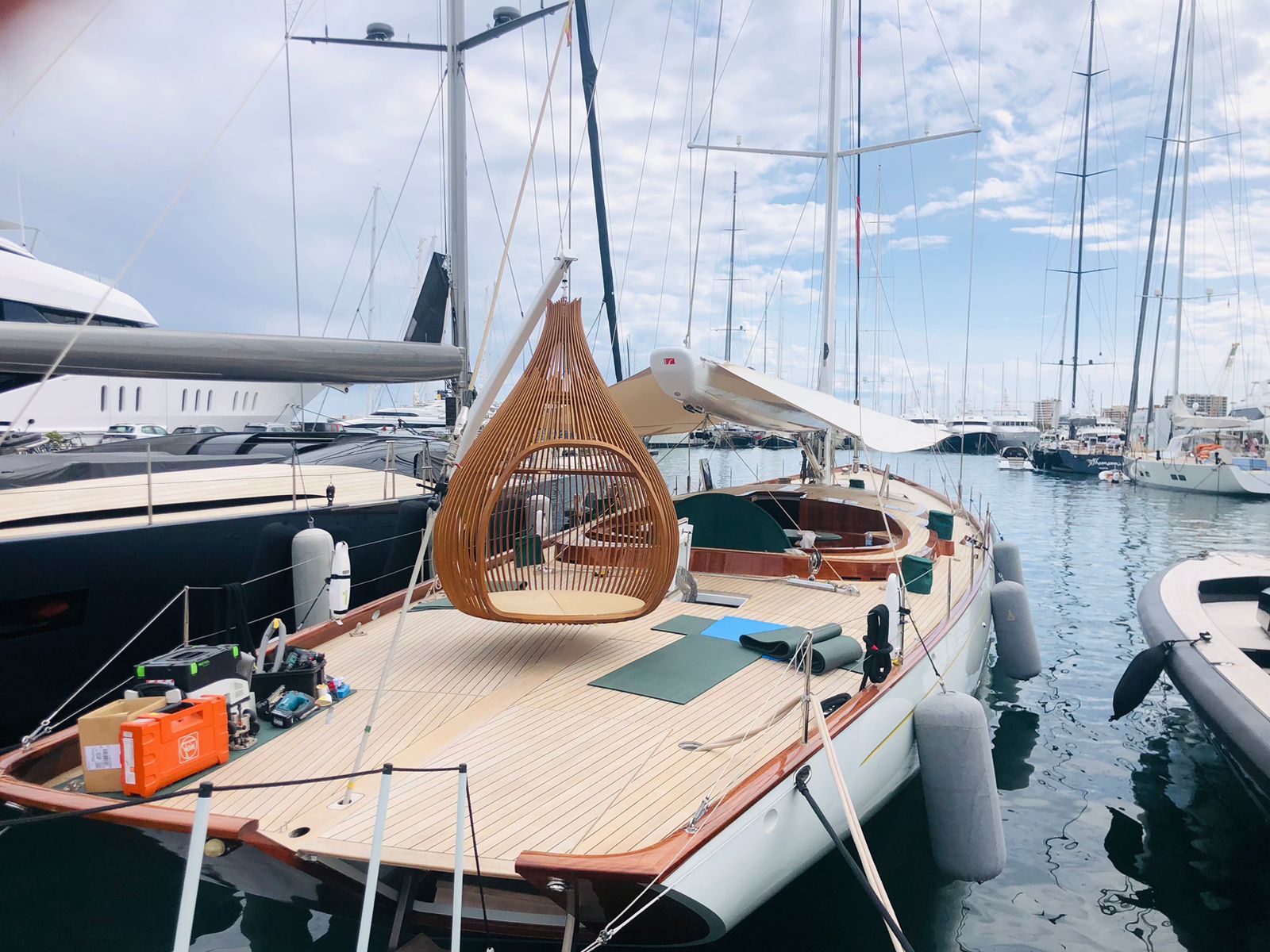
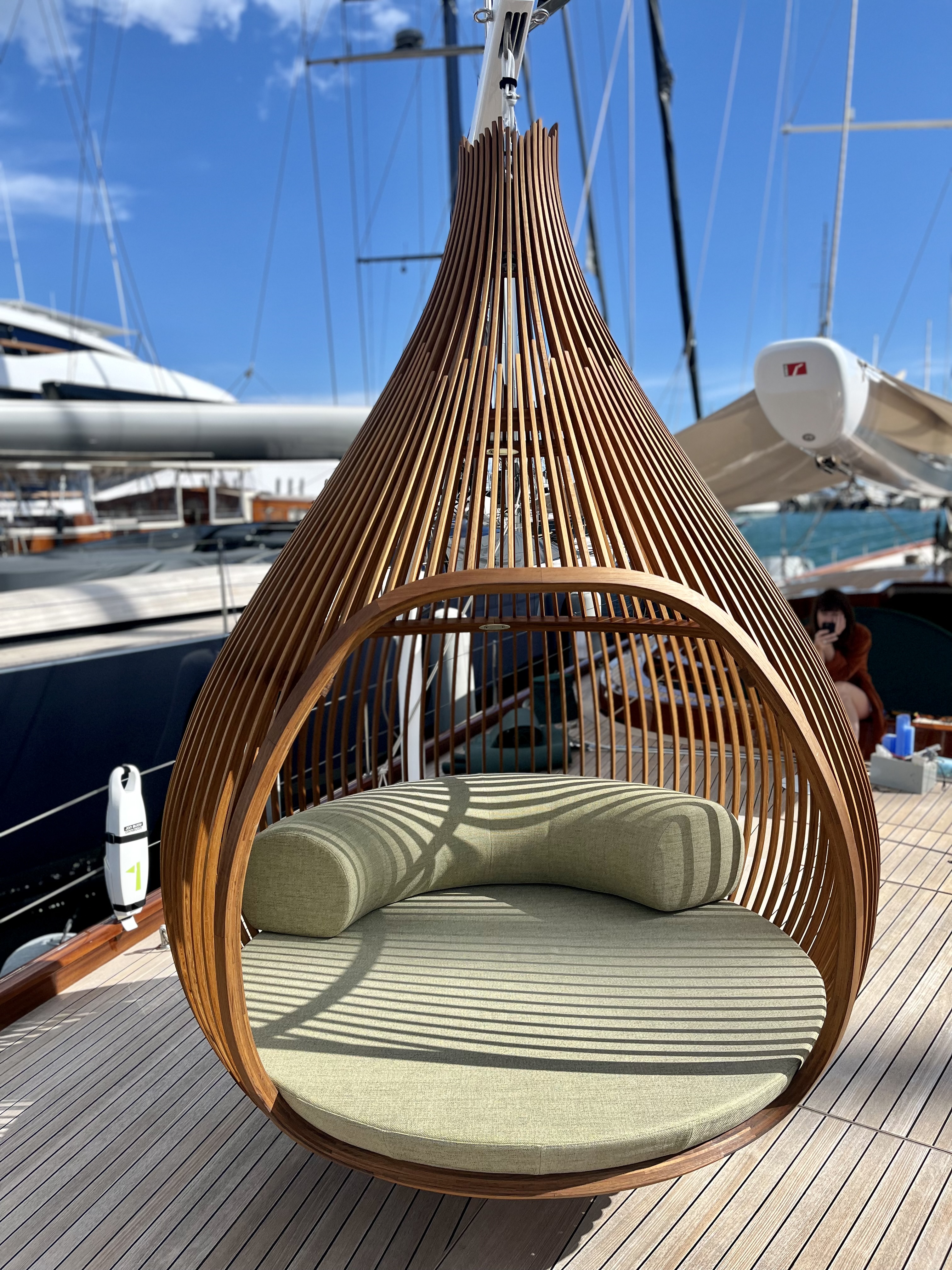
What do you want to do next?
Future Possibilities
Looking back on the project, Robert contemplates potential changes or improvements for future iterations.
"If designing for a location like a hotel where breakdown for storage is unnecessary, I would definitely consider creating the chair as a single, solid piece".
He also believes more parts could be produced using CNC machines, reducing manual labour and ensuring precision.
"I am very aware not to detract from the 'handmade' aspect of the build, but there are definitely areas within the build that CNC could be advantageous".
Furthermore, Robert envisions experimenting with different woods for interior chairs, such as walnut, to add variety to the chair's aesthetics.
In conclusion
The Teardrop chair is a testament to Robert's skill, perseverance, and collaborative efforts with partners like Cutr, resulting in a remarkable piece of furniture that seamlessly combines functionality and captivating design.
Would you work with Cutr again?
"It was great to partner with Cutr to overcome these challenges and the mould that the production partner delivered was perfect".
The production partner
No design is too crazy for Kleizen.
Their team of specialist engineers, craftsmen and machine operators have extensive experience and knowledge of complex shapes. Their expertise in the Maritime sector made them an obvious choice for the Teardrop Chair.
The result with Kleizen is always beautifully customised high-quality products.
Find your new production partner here
Additional photos
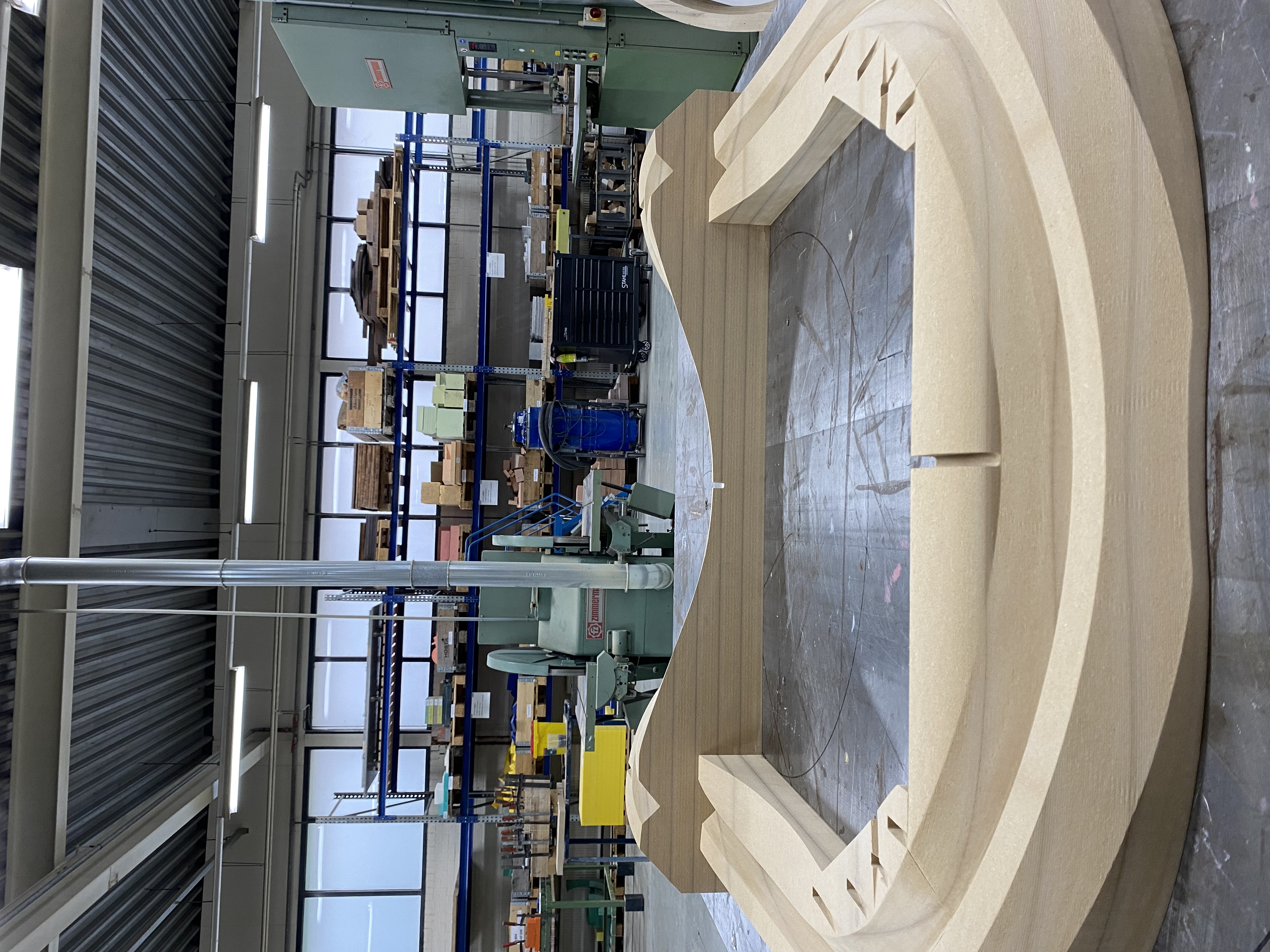
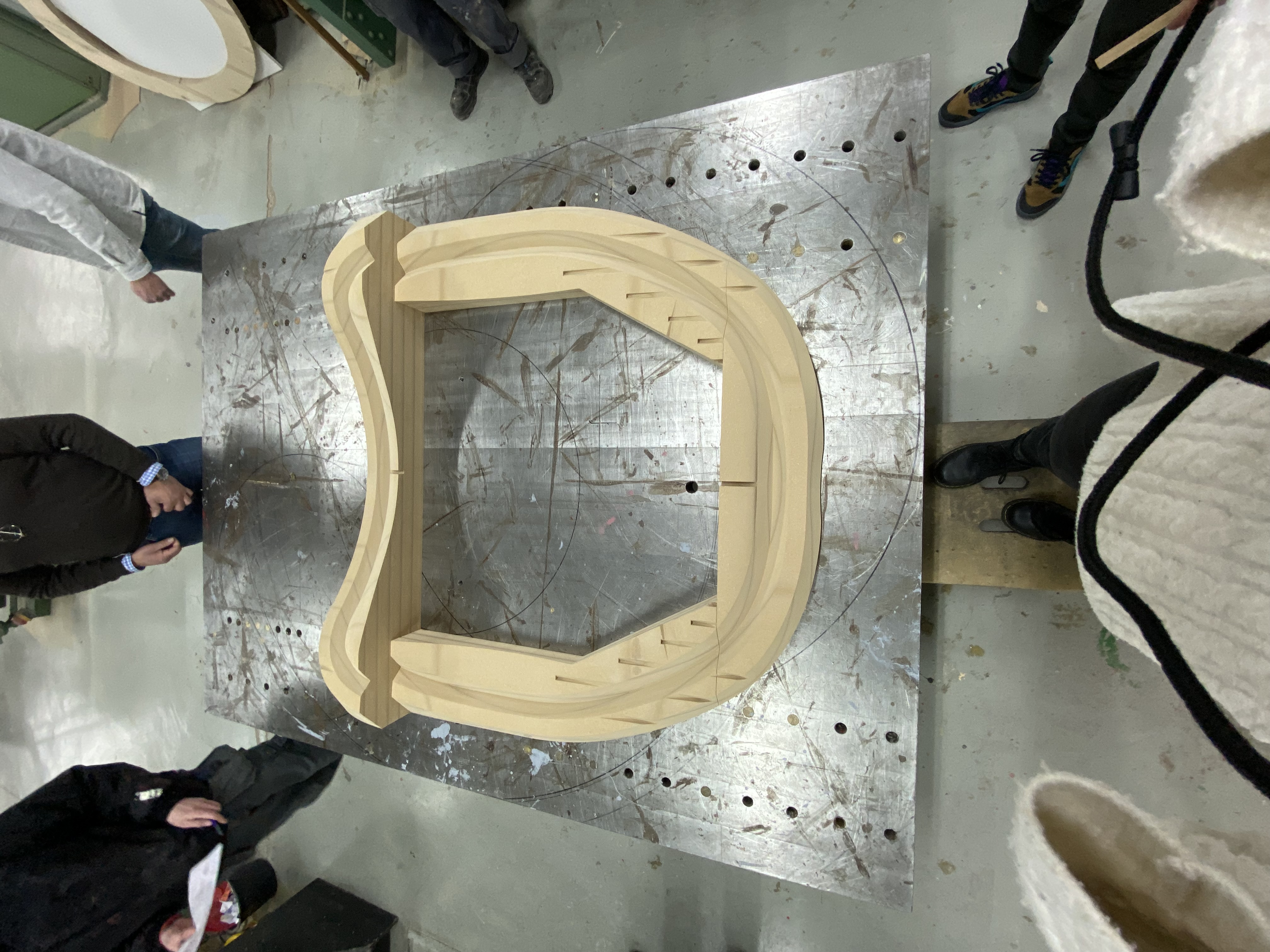
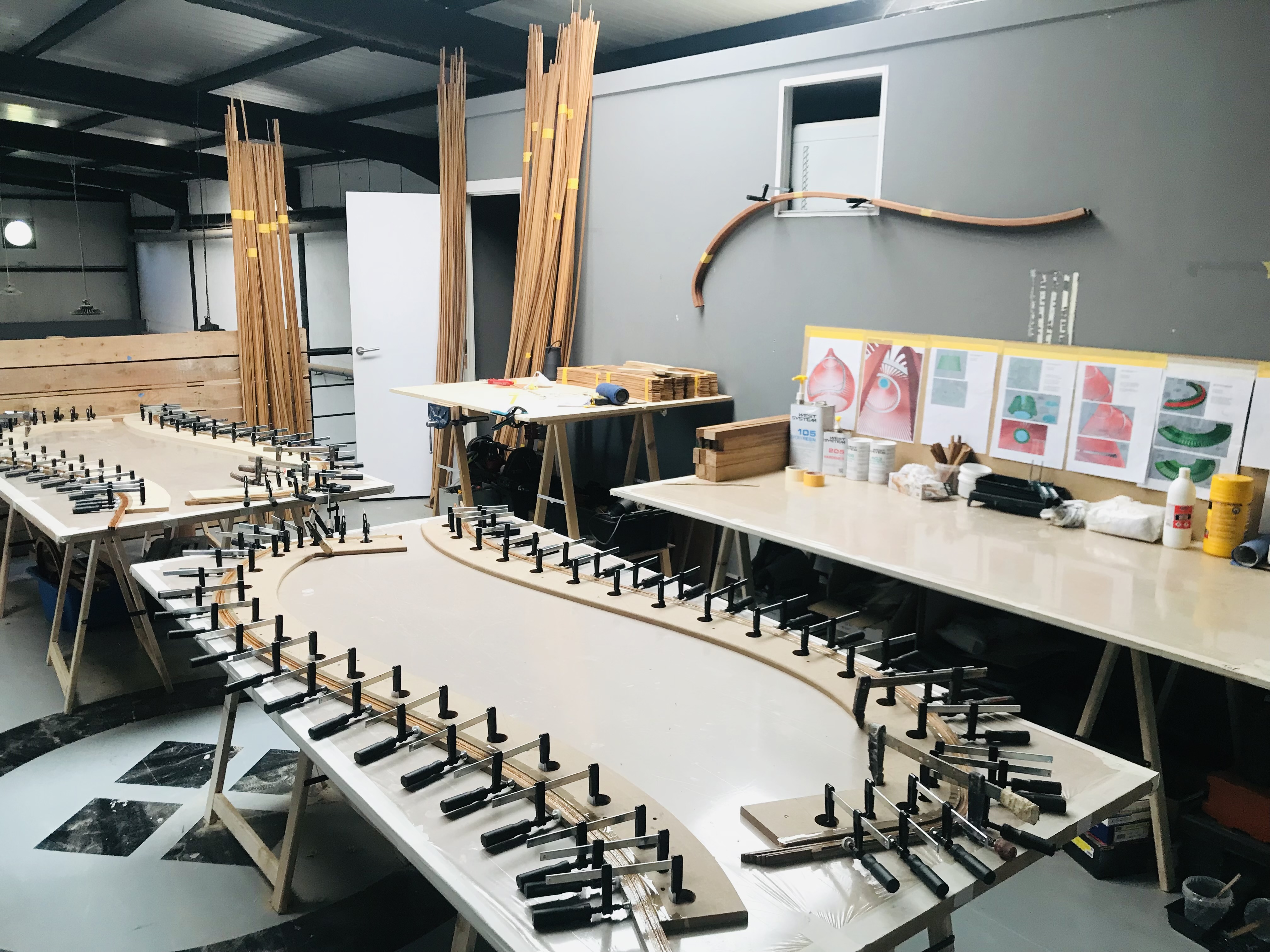
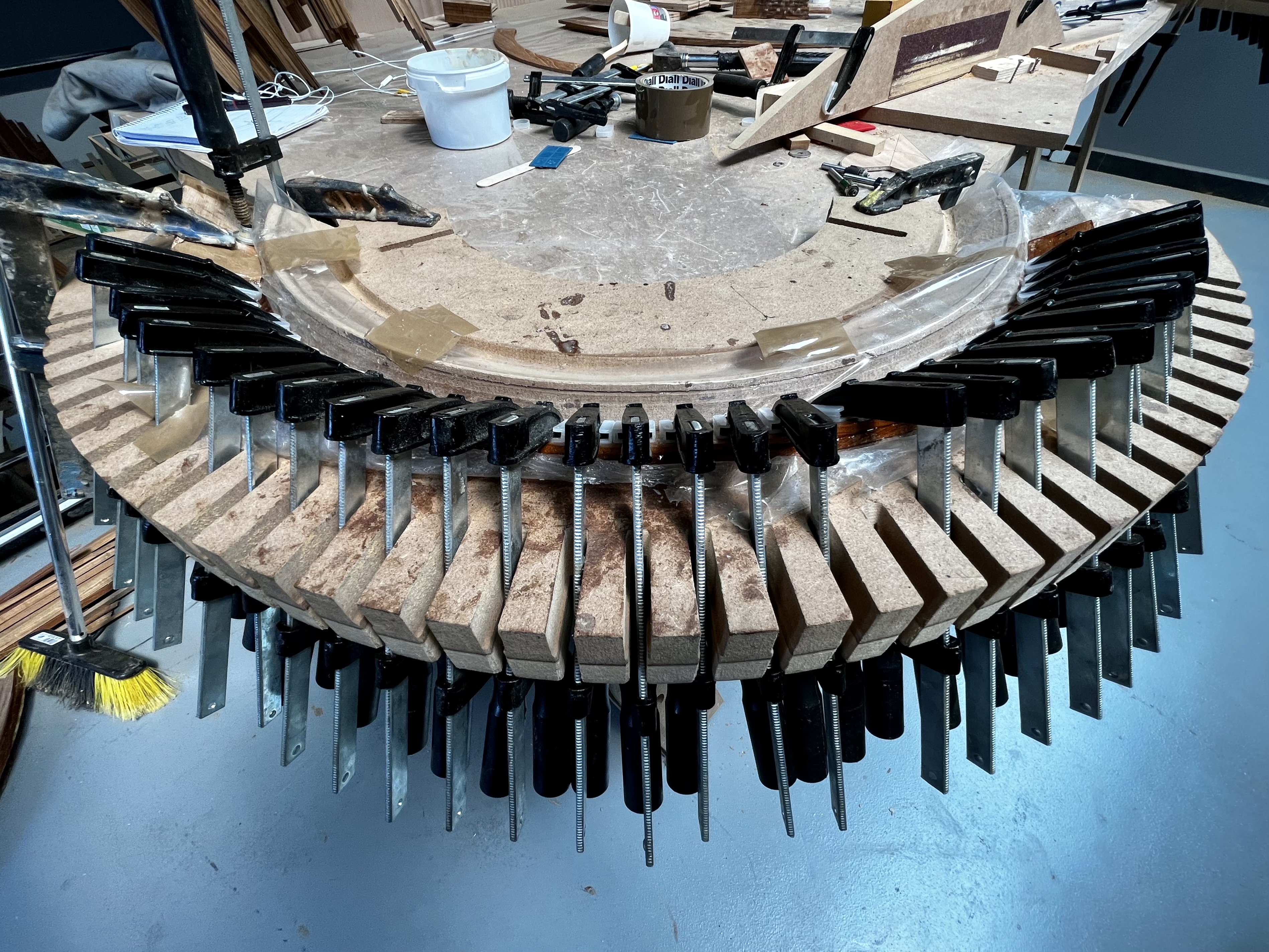
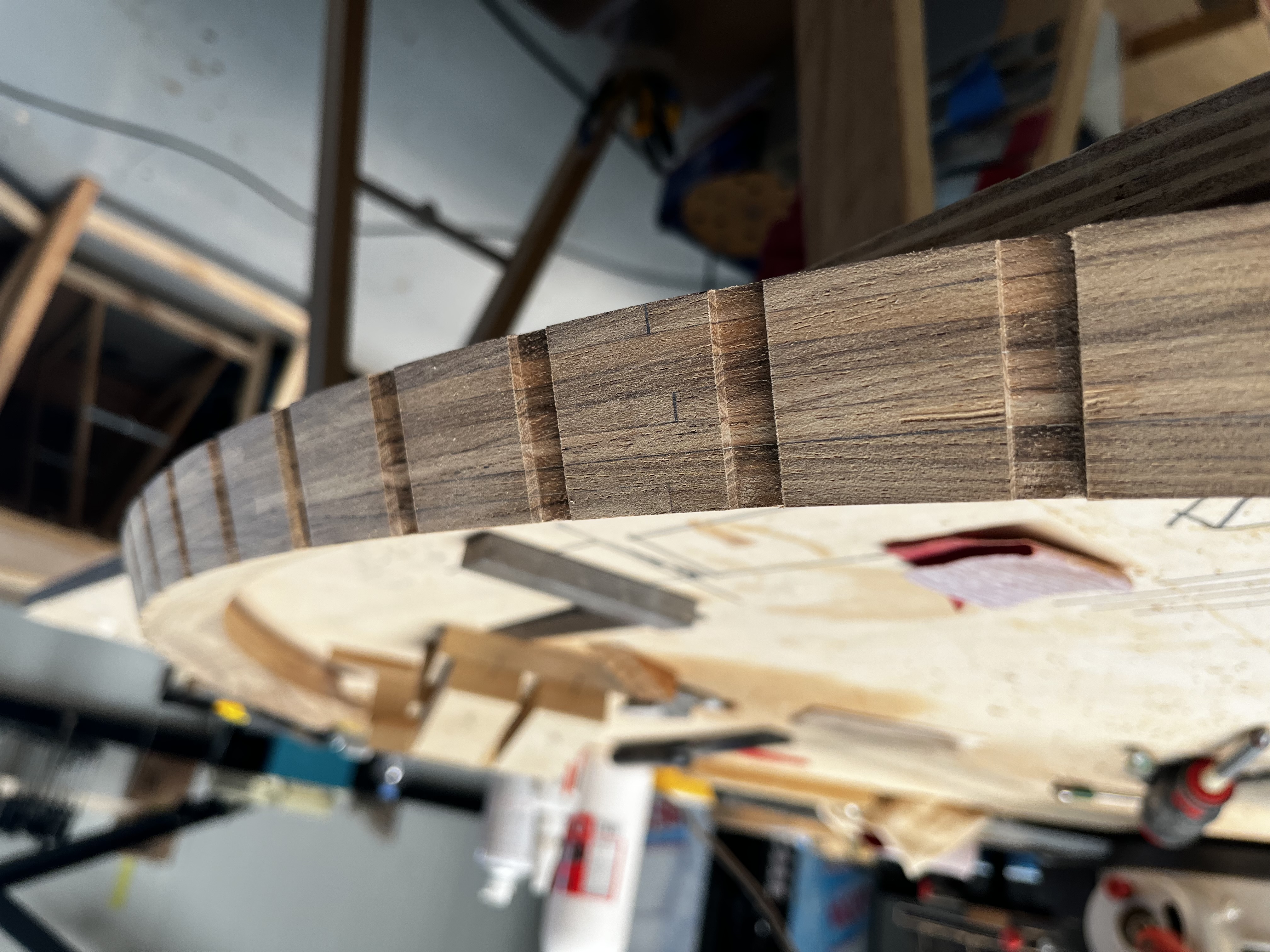
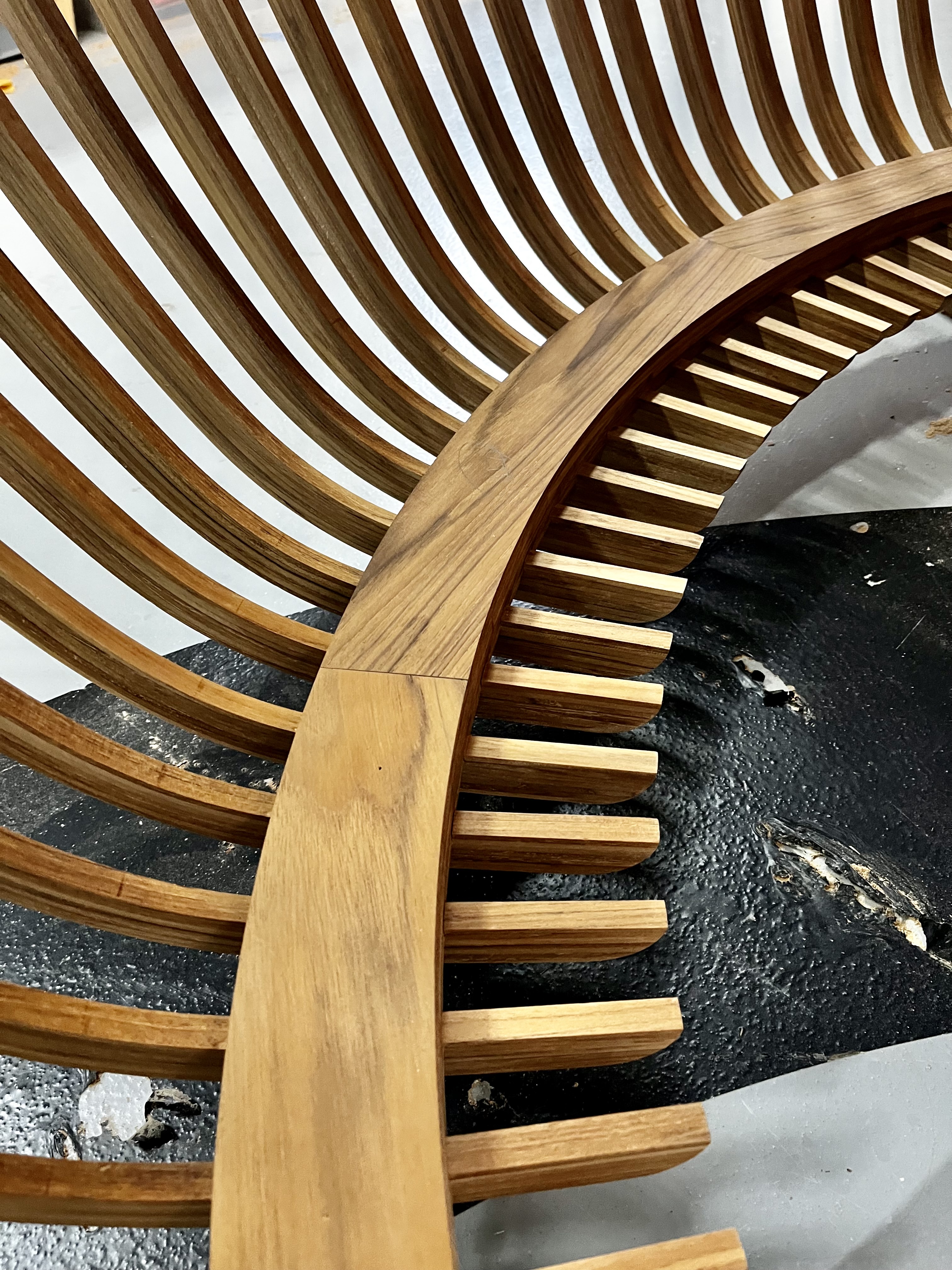
Upload your design file and get a quote
within days
Quality production with trusted production network.
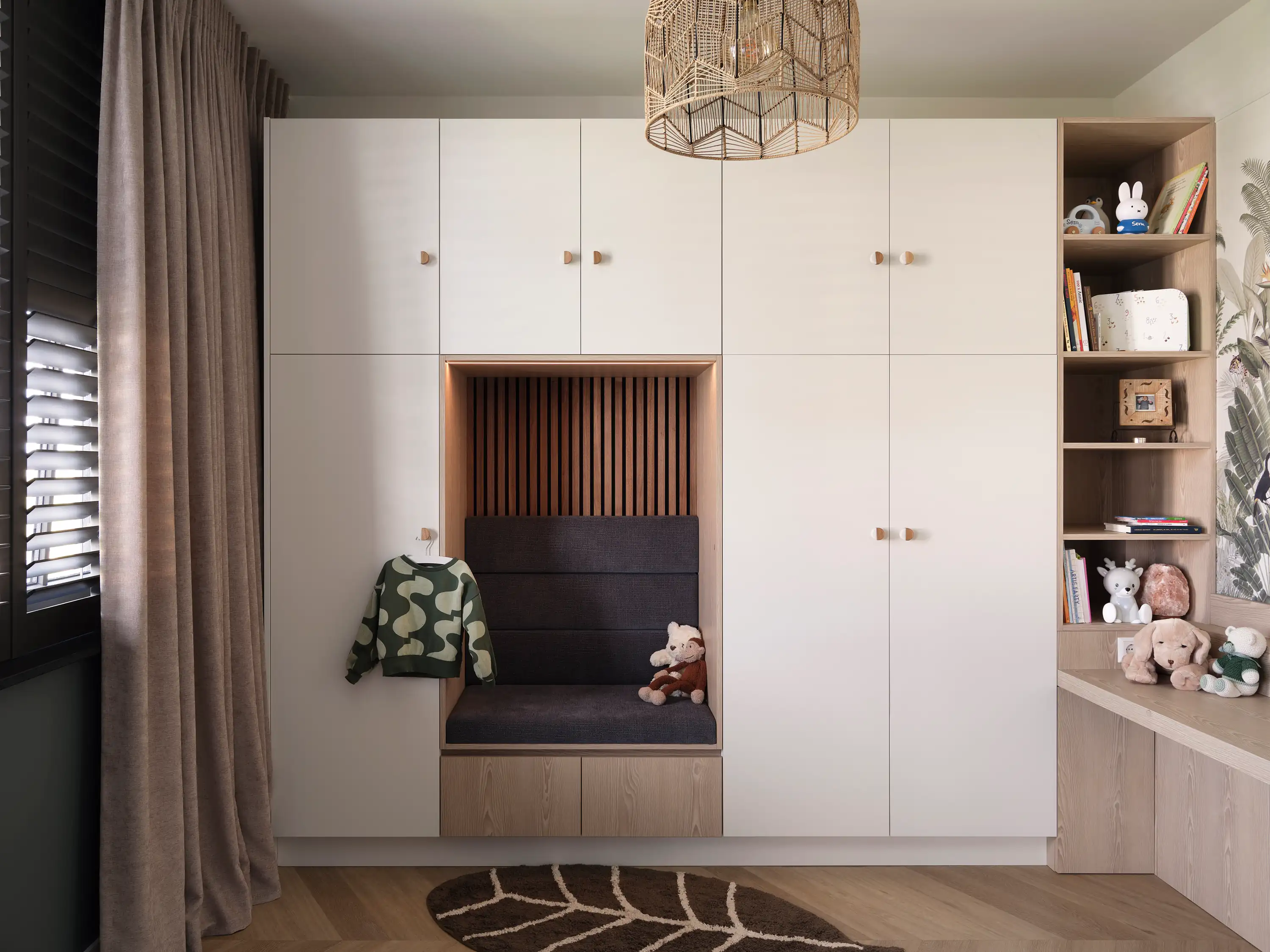
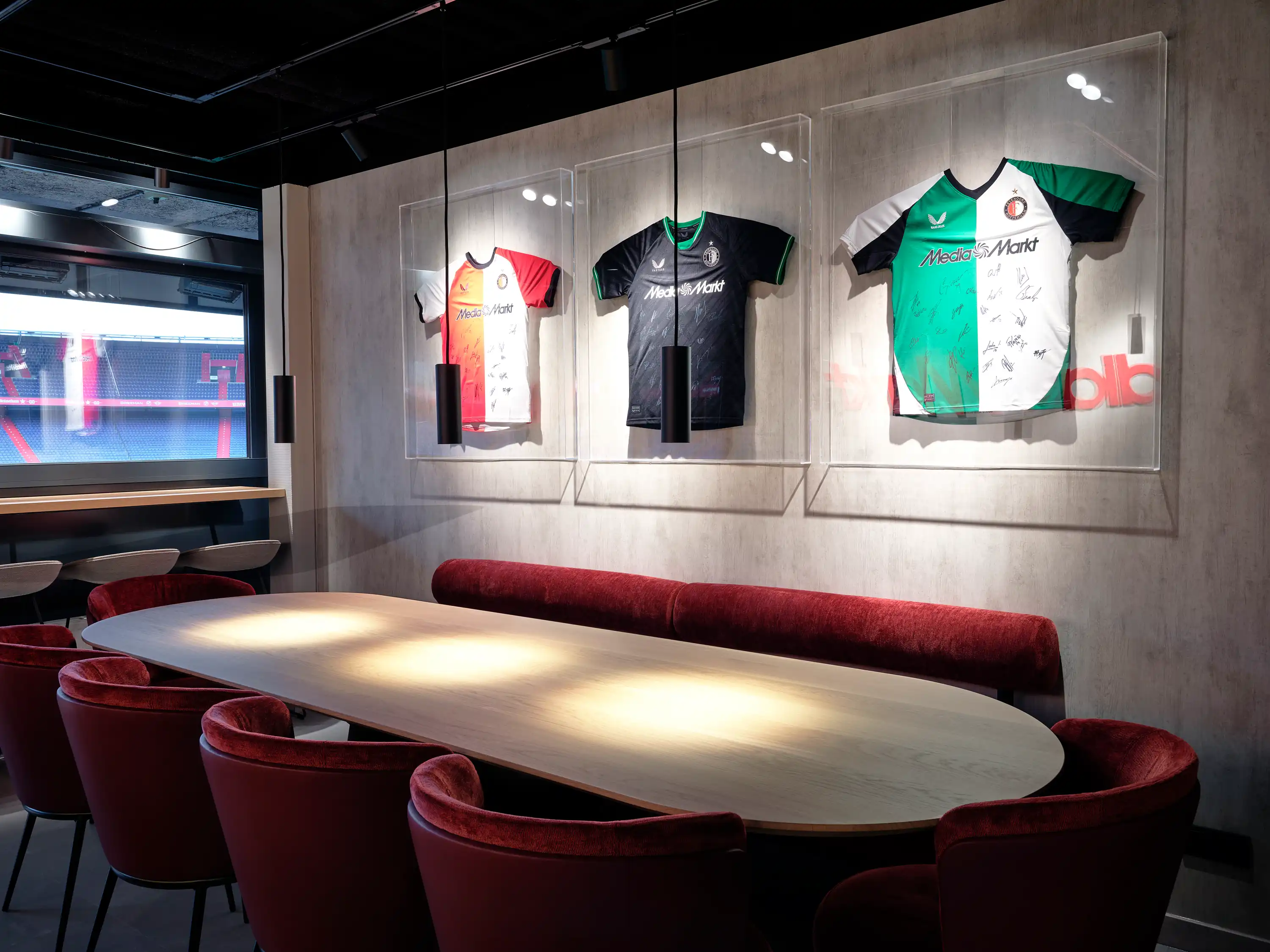
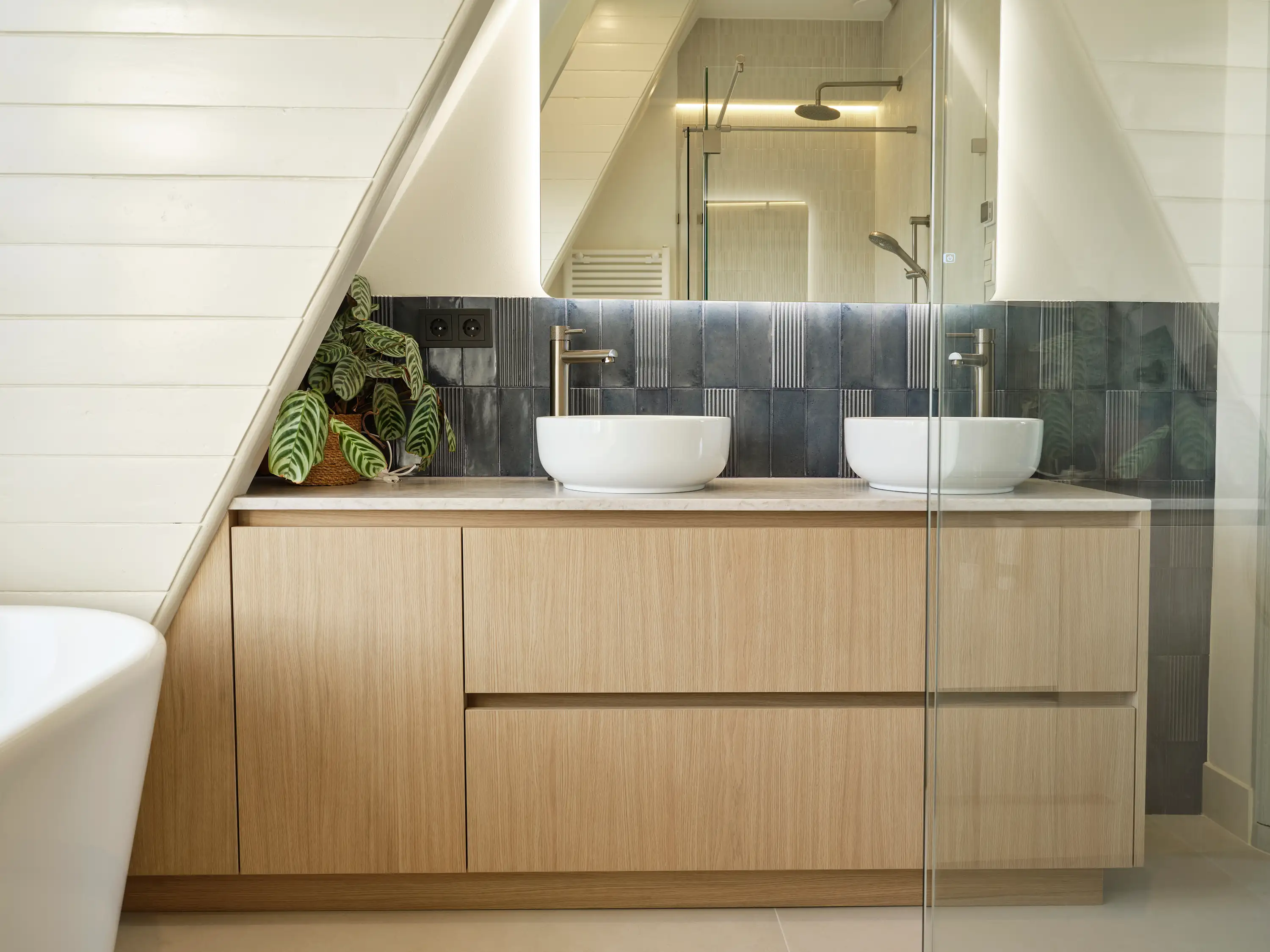
%20(1).webp)
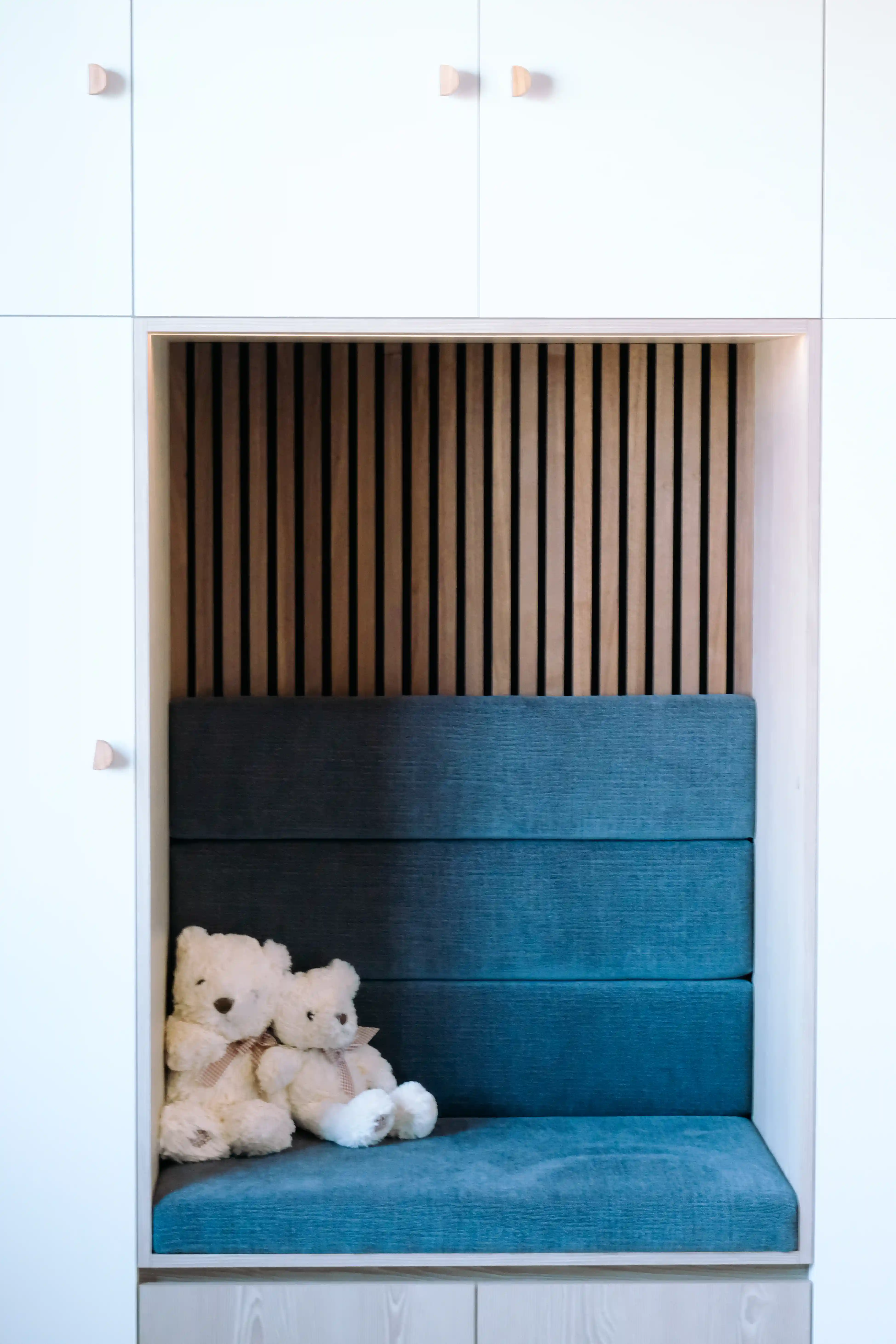
.webp)
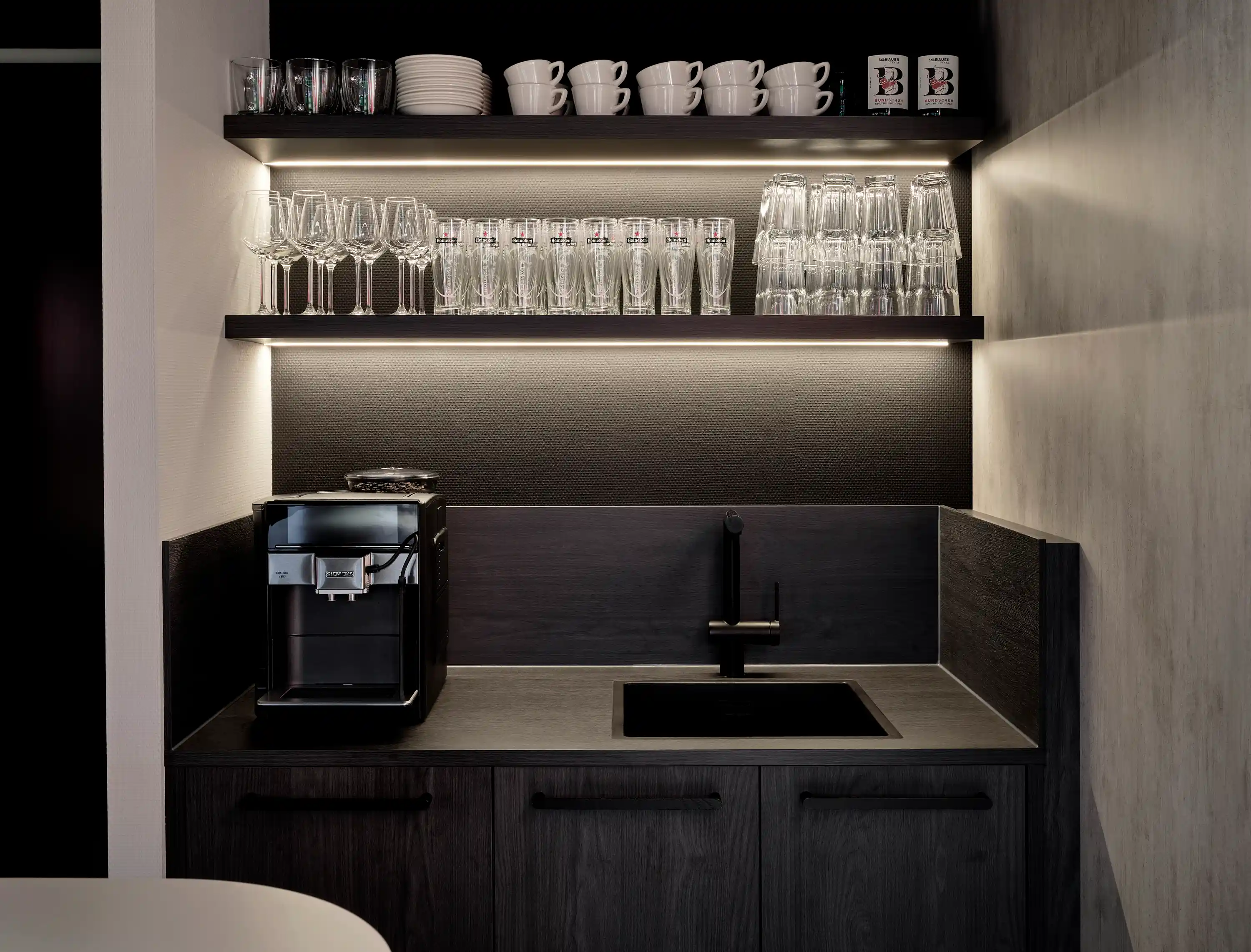
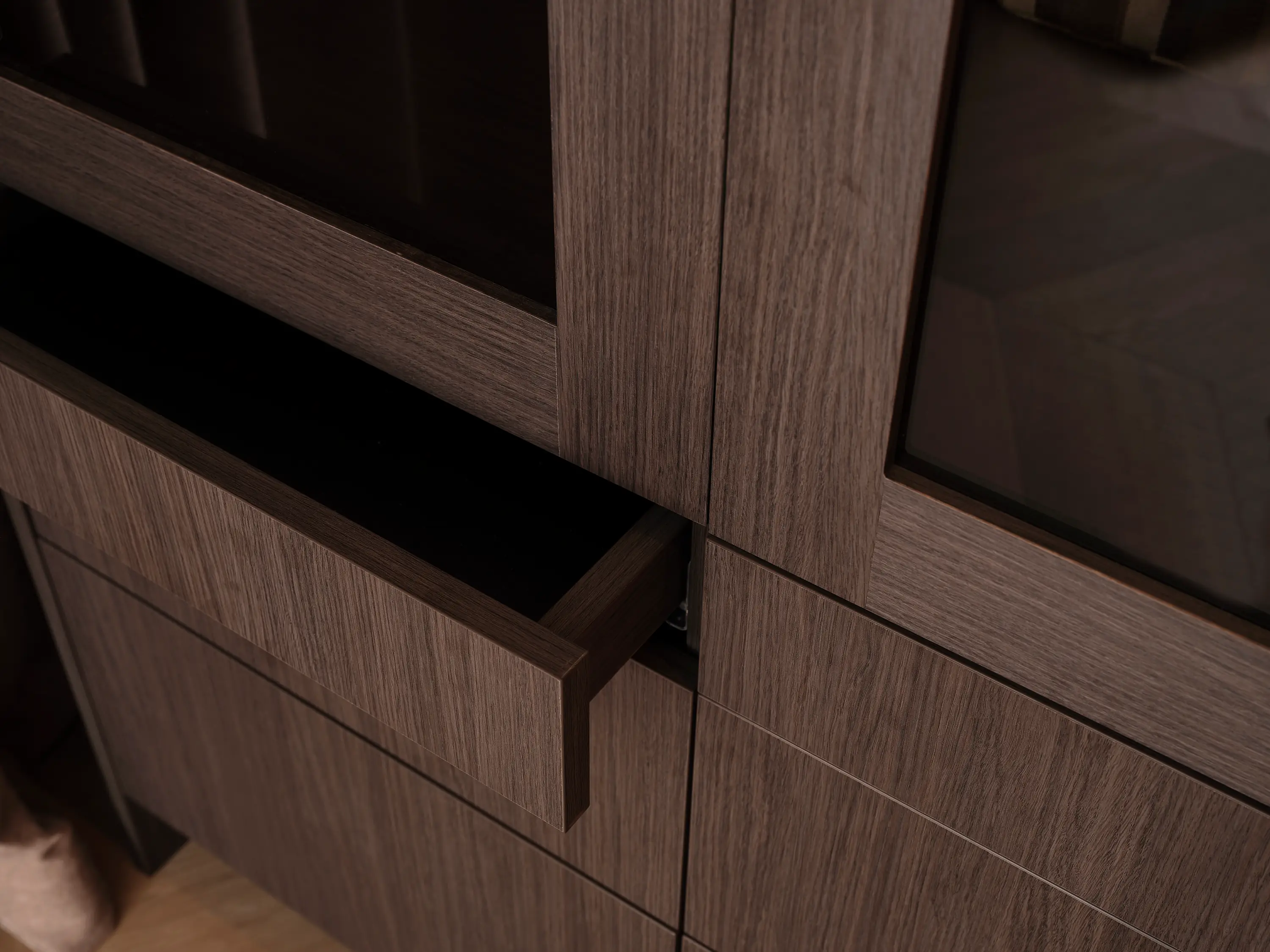
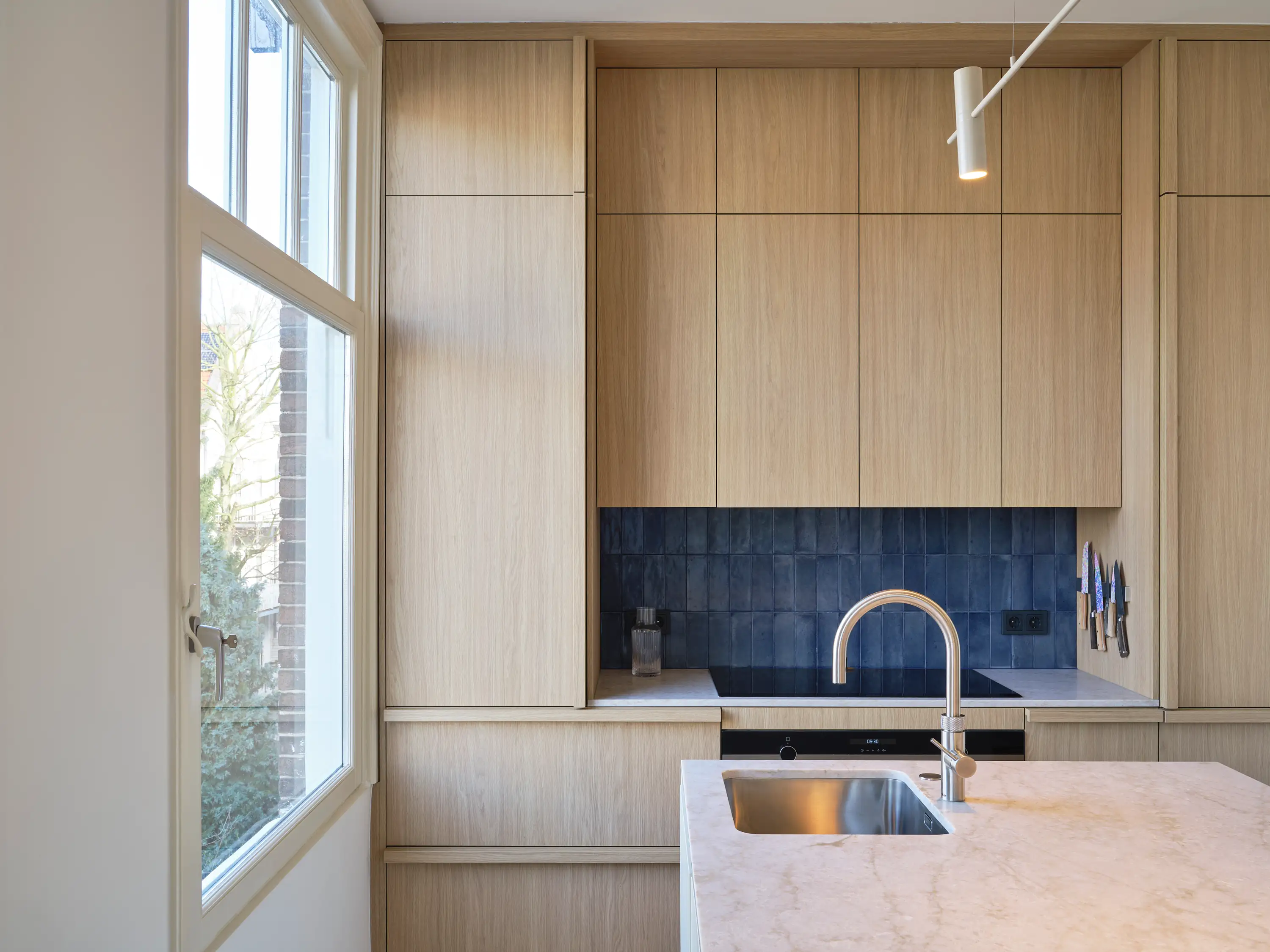
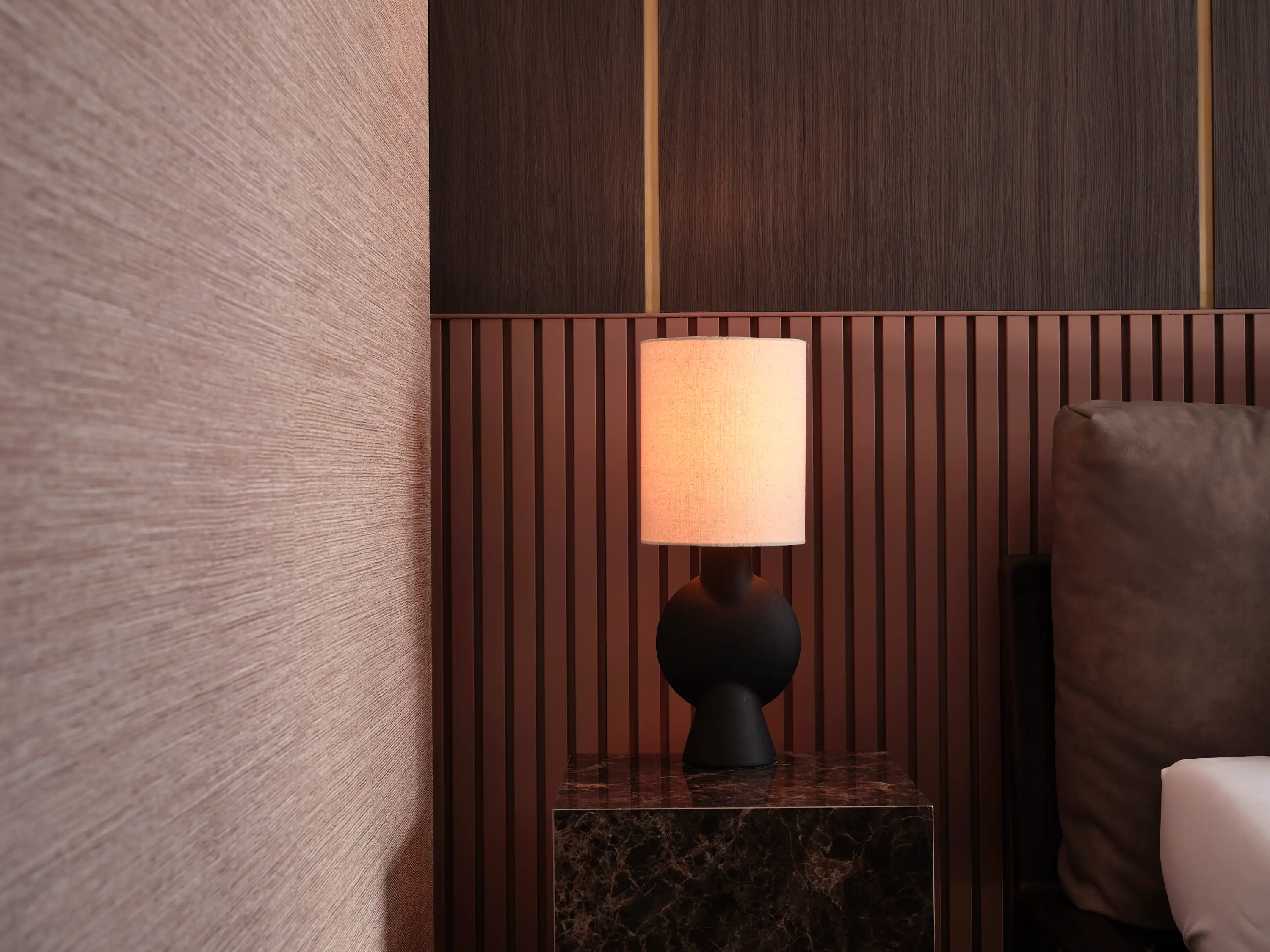
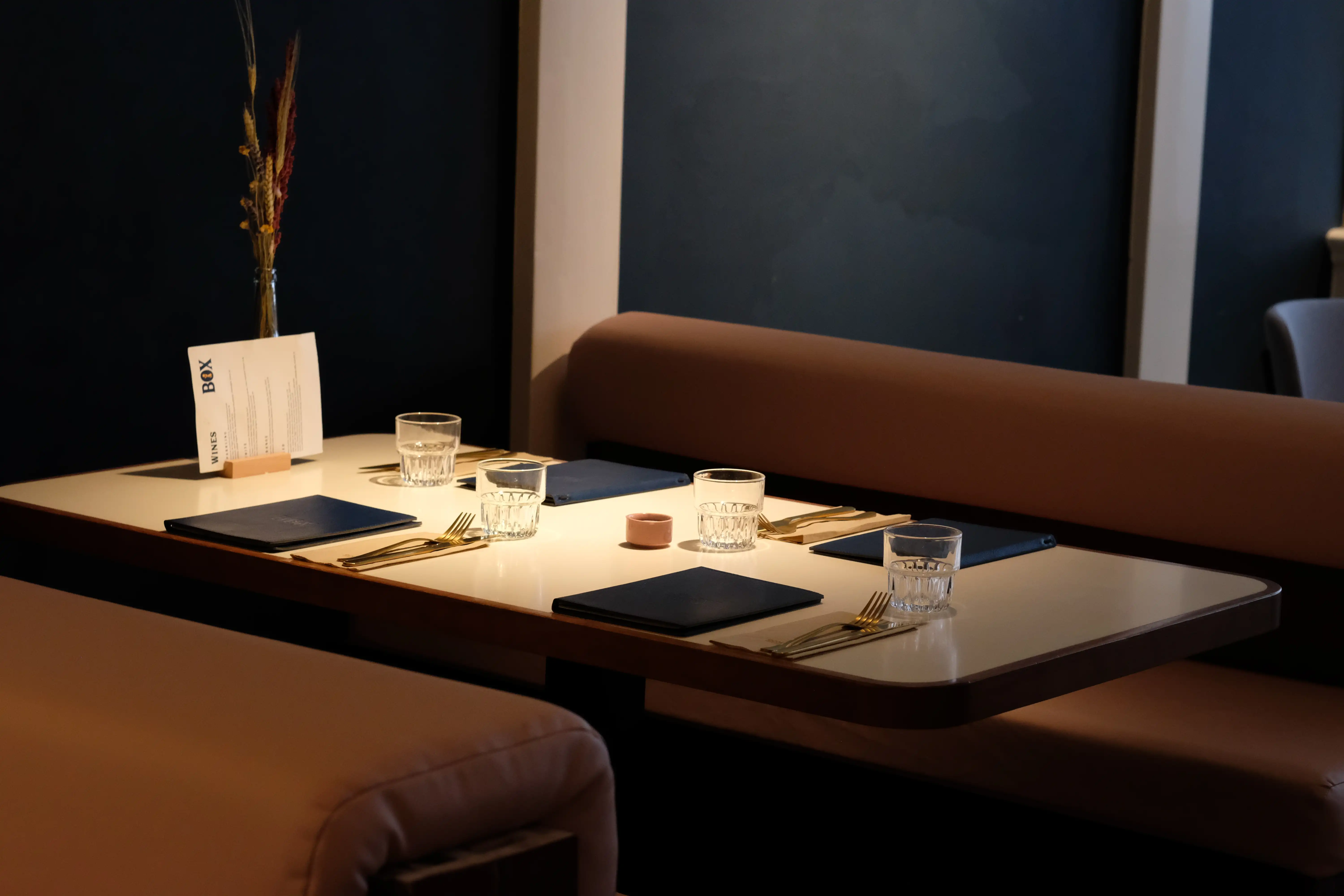
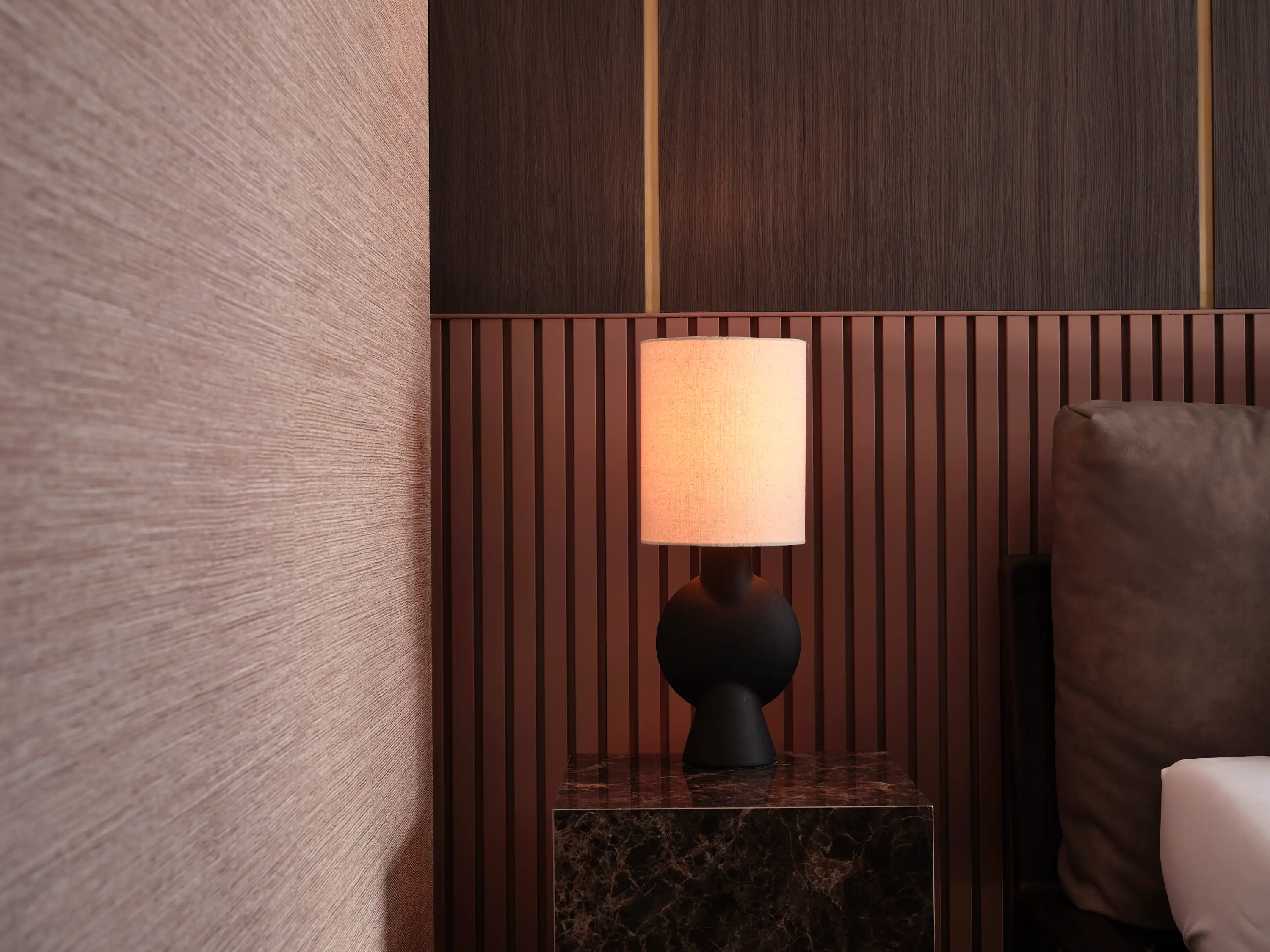