The Top 3 Reasons for Production Process Delays and Its Solution (Interior Projects)
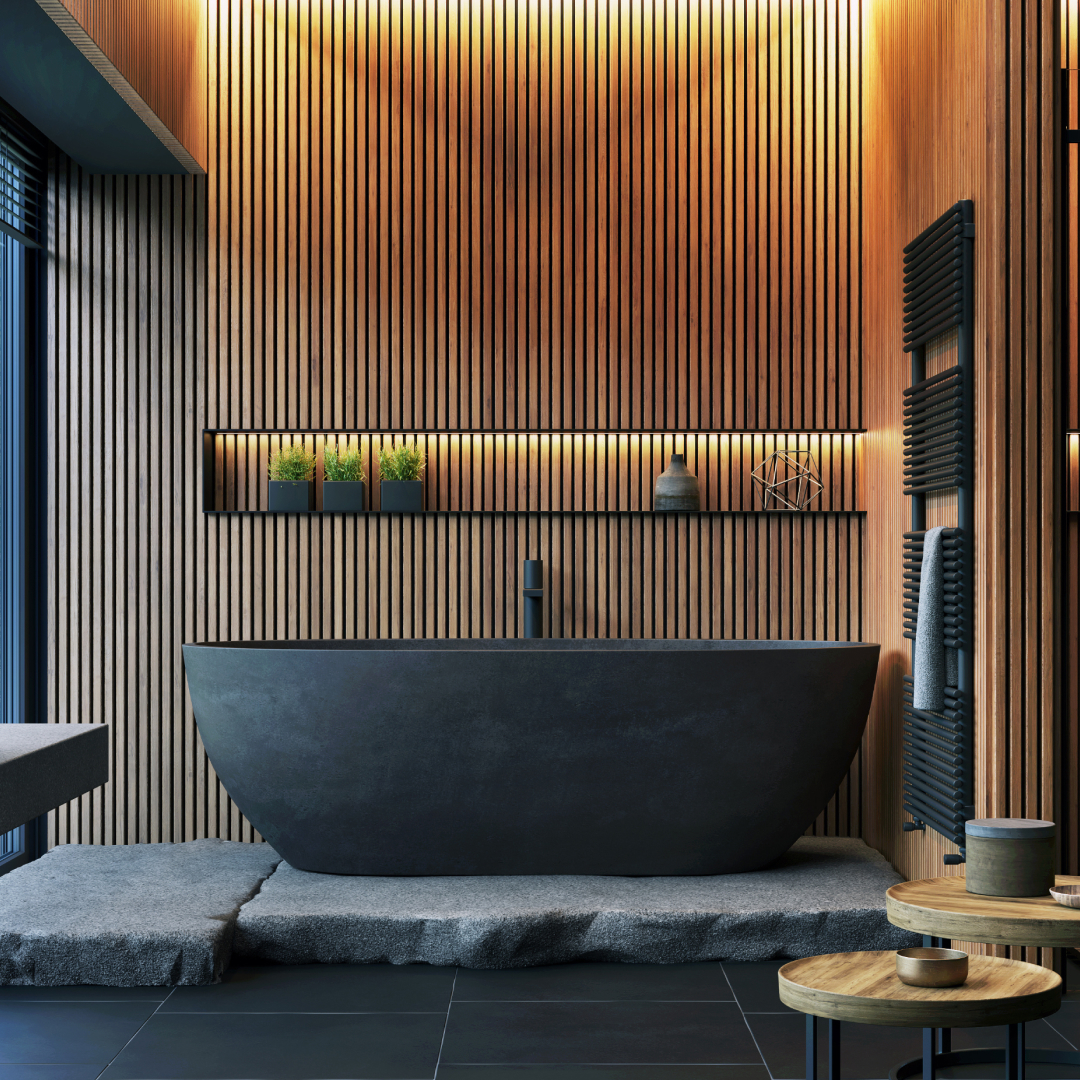
Why do architects and product designers often experience delays for their interior projects?
Interior projects can be delayed for a variety of reasons, including:
- Materials not being delivered on time
- Materials damaged during delivery
- No delivery of materials at all
In all three cases, this means the material has to be reordered or replaced, which means extra costs, effort and time.
Another reason for delay might be that errors were made by either machines or personnel during production. Such production errors may sometimes seem harmless, but they can easily disrupt your planning.
Use of blunt tools can also contribute to damage during the production process, which in turn can delay the delivery time of the project. In addition, sometimes measurements aren’t taken properly and the material doesn’t fit through the door. Quite embarrassing, of course, but it's a common occurrence.
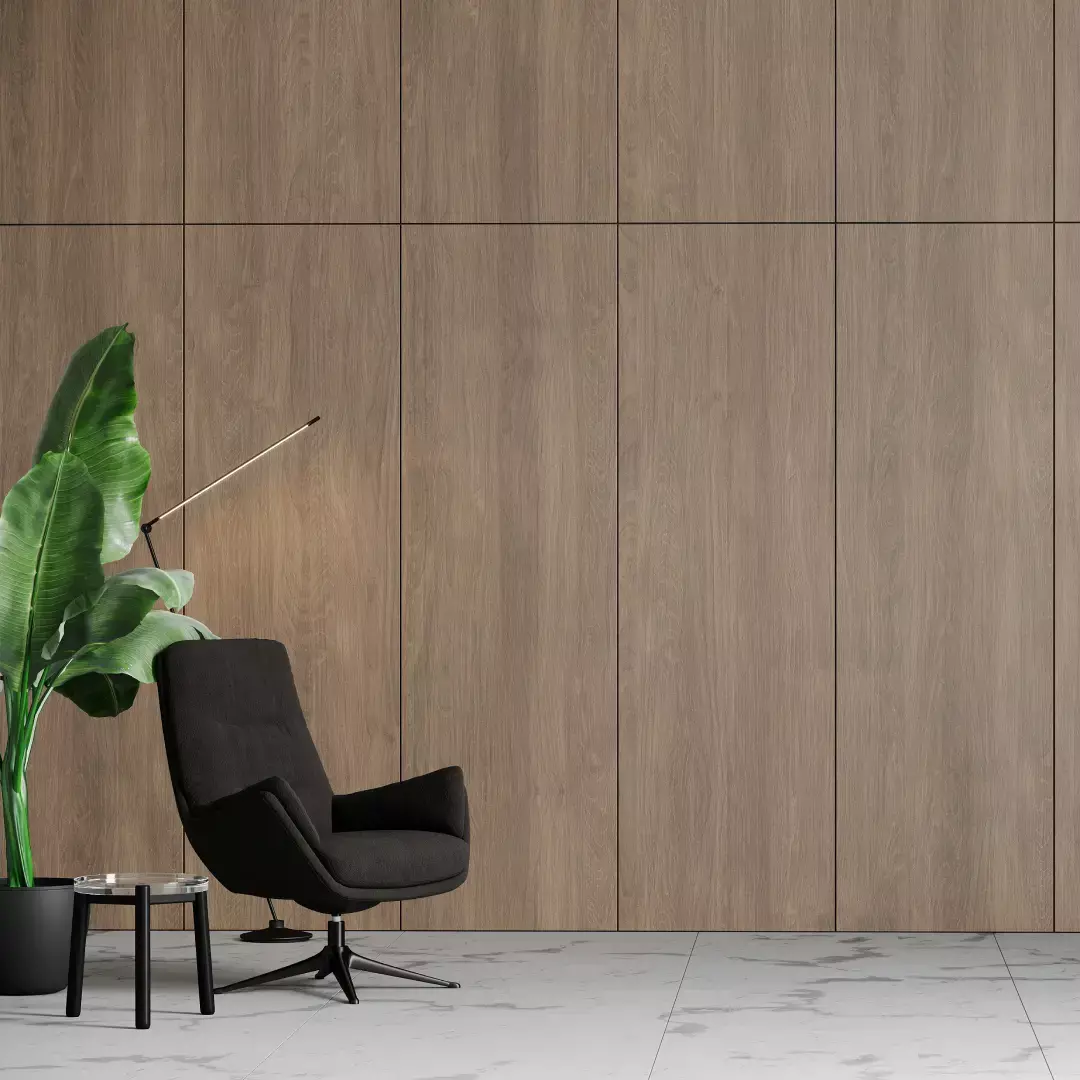
Besides the above, if tolerances weren’t used, this could lead to issues during installation. As you can see, there are multiple potential problems that might cause serious delays for interior projects.
How can fast and accurate quotes reduce these delays?
Things often already go wrong when architects, interior- and product designers receive quotes for their interior projects. Inaccuracies in quote requests can lead to errors and associated delays further down the production chain.
There are a couple of ways you can minimise the risks during these RFPs:
- By adding 3D models that are as detailed as possible, there is less chance of errors
- Tolerances and fitting laths can be taken into account by drawing in spaces
- Using proper checklists can help prevent errors related to the location itself
These steps may seem entirely logical, but too often they’re still skipped. A 1-hour investment in preparation of the work can quickly save up to 3 hours in the workshop.
When the quote request process for wooden interior projects contains the three points mentioned above - which is the case with Cutr - we see projects being manufactured and finalised 3x faster, on average.
What else is important for keeping the interior project production chain streamlined?
Getting your wooden interior projects finalised quickly involves more than just working with fast and accurate quotes based on 3D models. You also have to be careful that you work with:
- Drawings that are correct
- Correct naming (stickers)
- The right steps in your planning process
Keep thinking ahead while you're preparing the work and make sure to schedule in some buffers to minimise the risk of delays. Purchase the right materials and make sure the delivery of semi-manufactured products takes place in time.
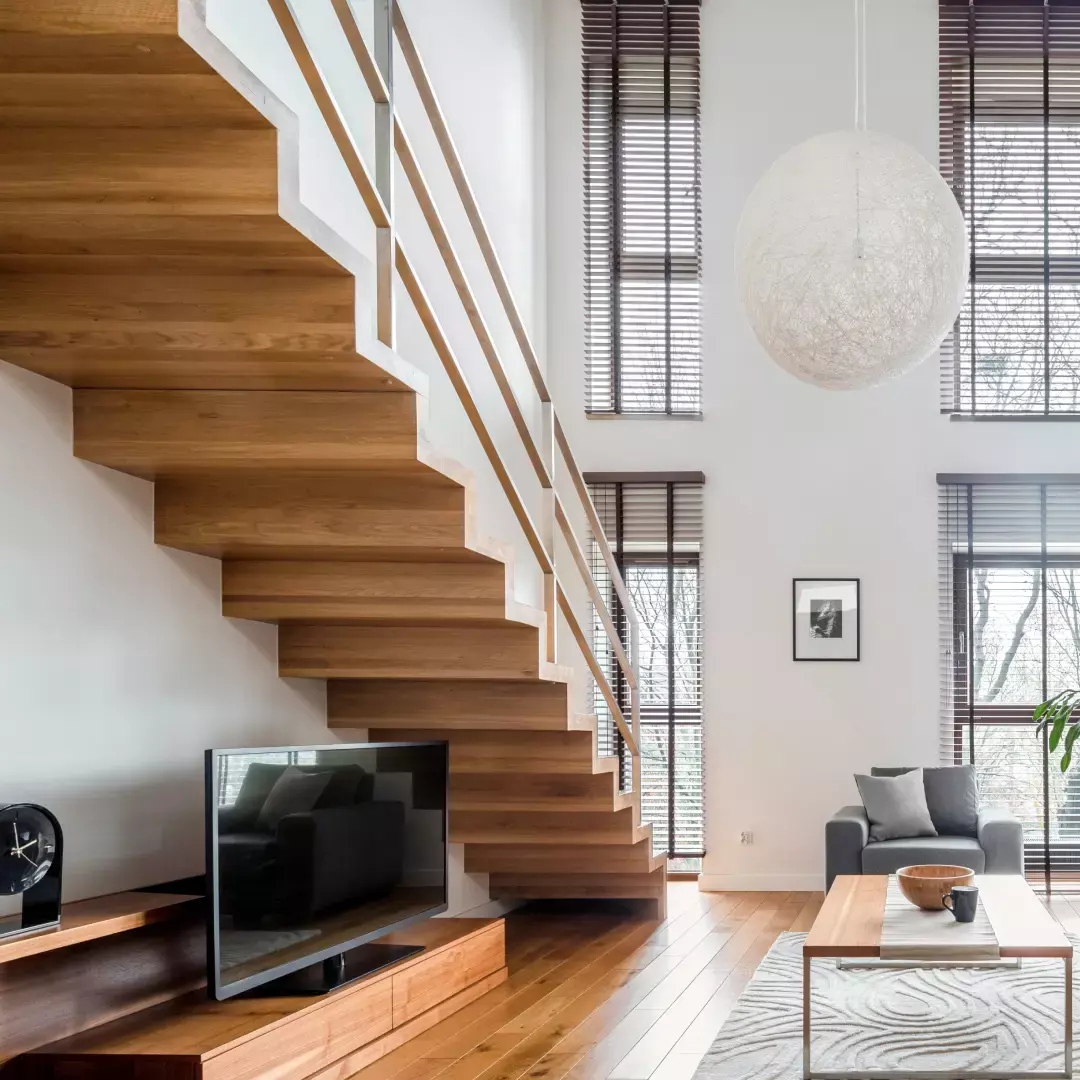
Additionally, it’s important CAD- and CAM systems are integrated properly and communicate with each other in the right way.
Do you work with an ERP system? You would do well to ensure your ERP easily connects to drawing- or other software you use during your preparation.
But apart from these systemic requirements, you also need to take into account some more fundamental optimisations to your planning. For example, try scanning for next steps in the process early on, make sure tasks are being checked, and that you have central access to all data regarding inventory and deliveries.
This way, your wooden interior projects can get started early. It will also be easier to subdivide those projects into clearly defined steps.
Conclusion
Taking all these factors into account makes it much easier to deliver wooden interior projects on time. Do you currently have a wooden interior project that needs to be finished on time? Upload your design and get a free quote by clicking the button below.
Find out more about our manufacturing services here
Related articles:
A guide to 2D error free files
How can I get my wooden parts delivered as fast as possible?
Upload your design file and get a quote
within days
Quality production with trusted production network.
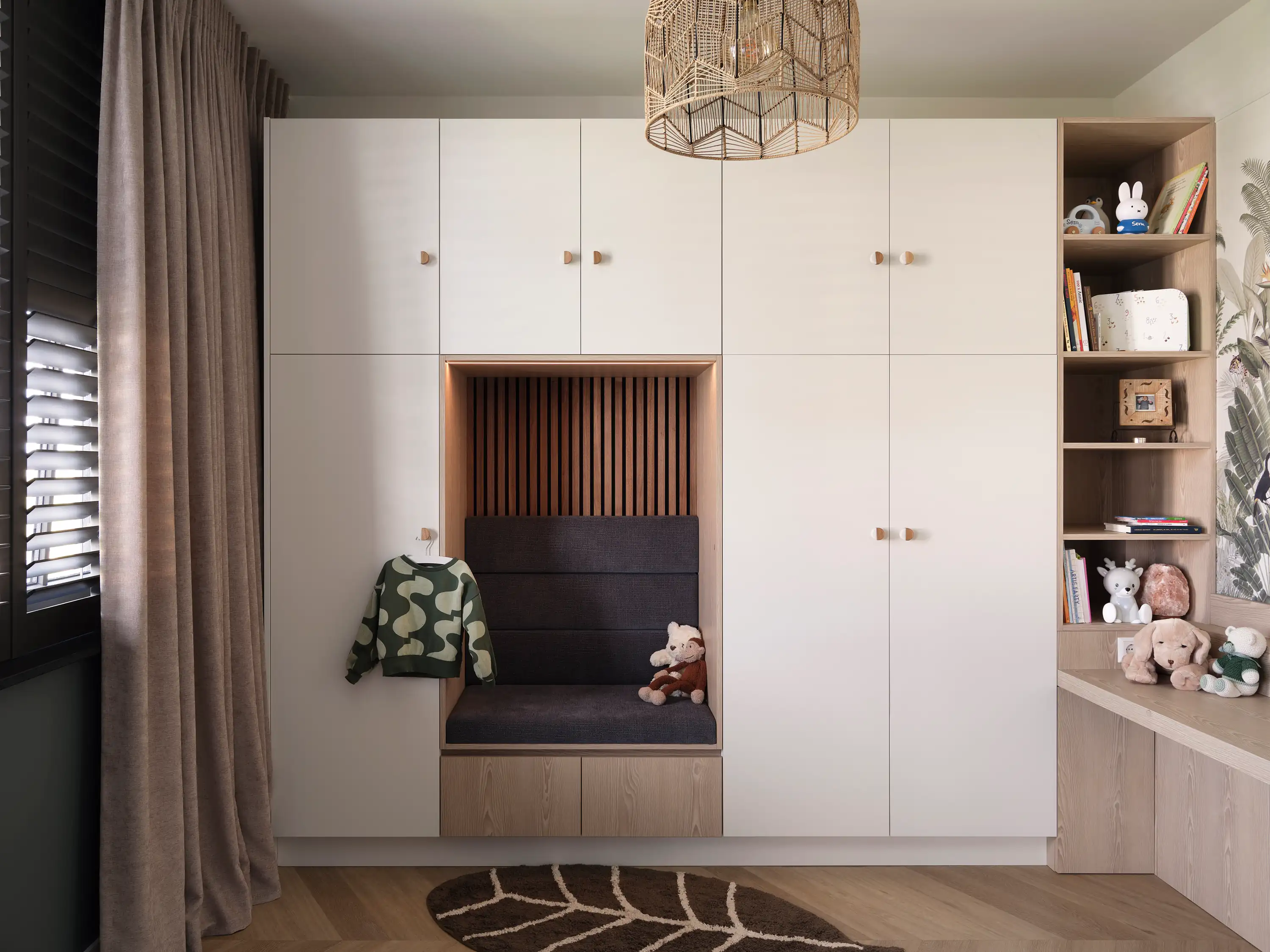
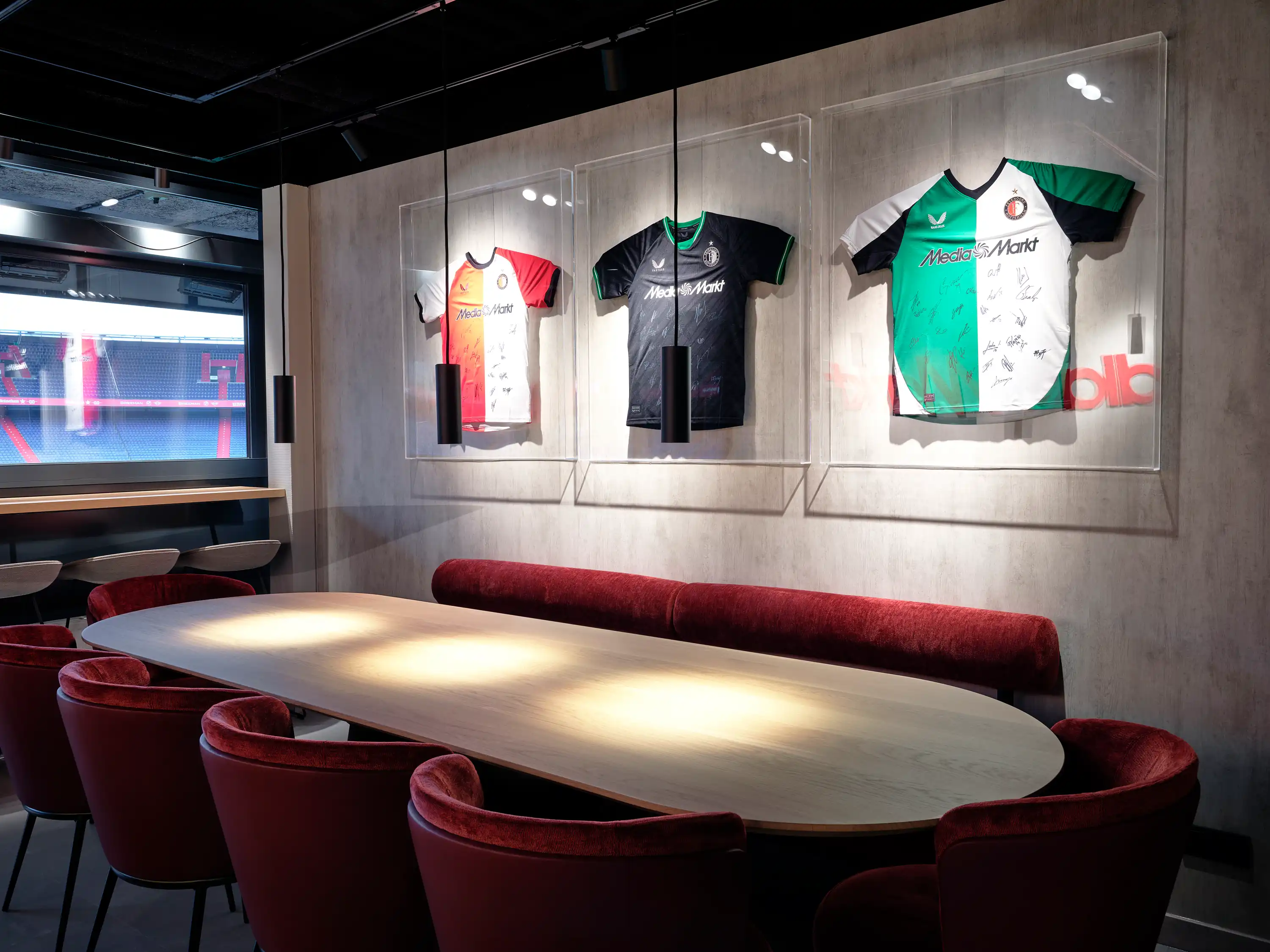
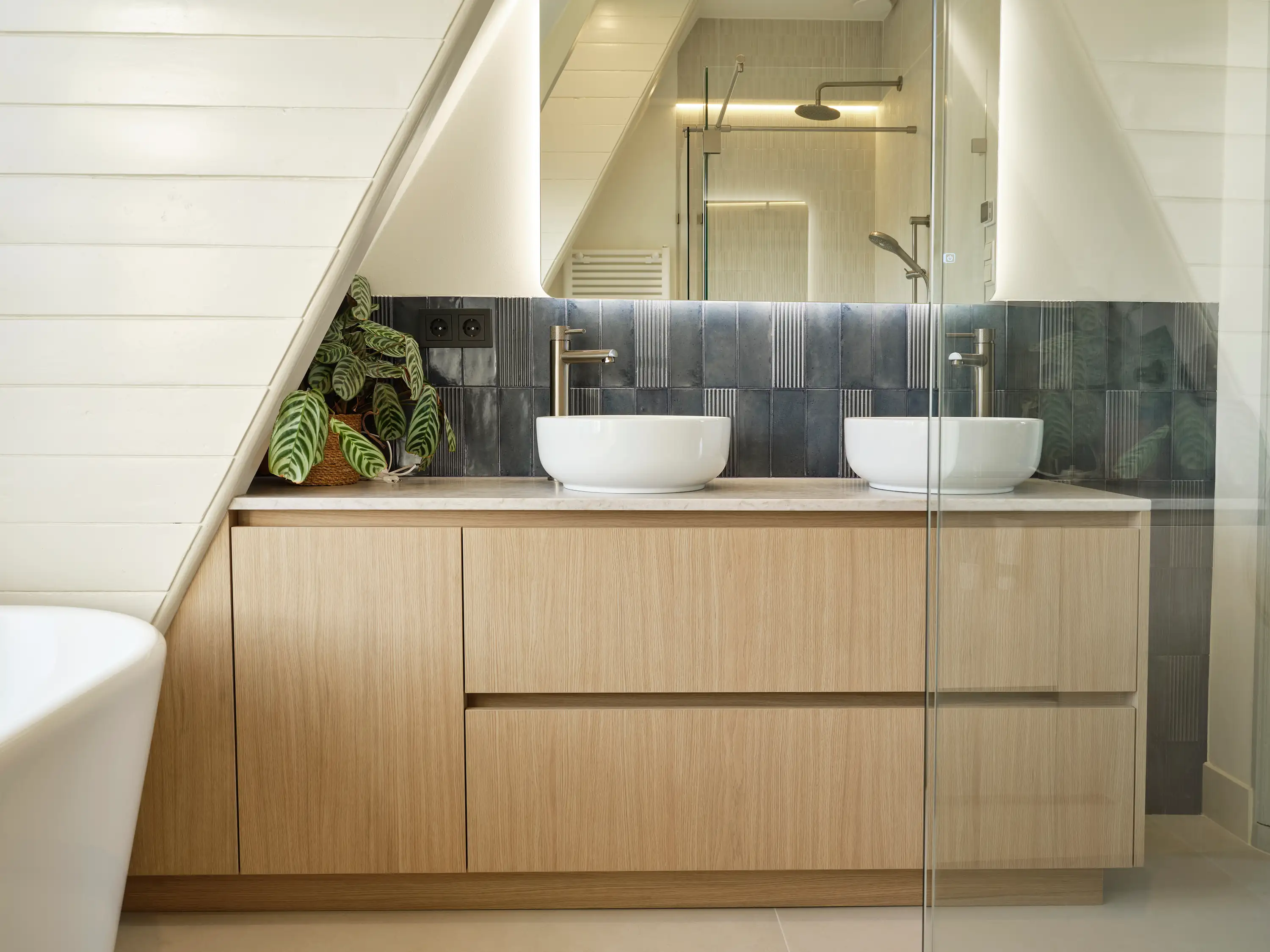
%20(1).webp)
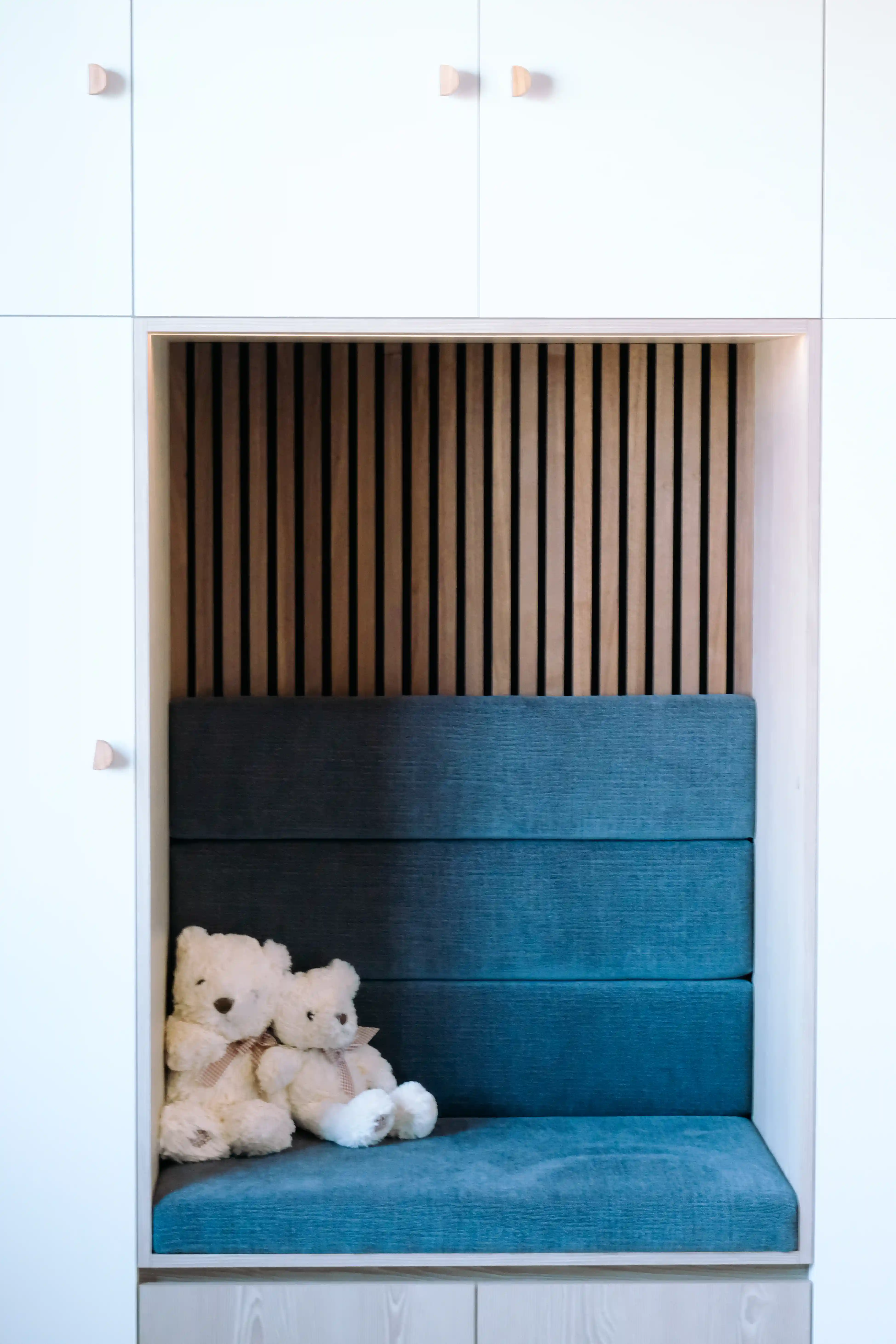
.webp)
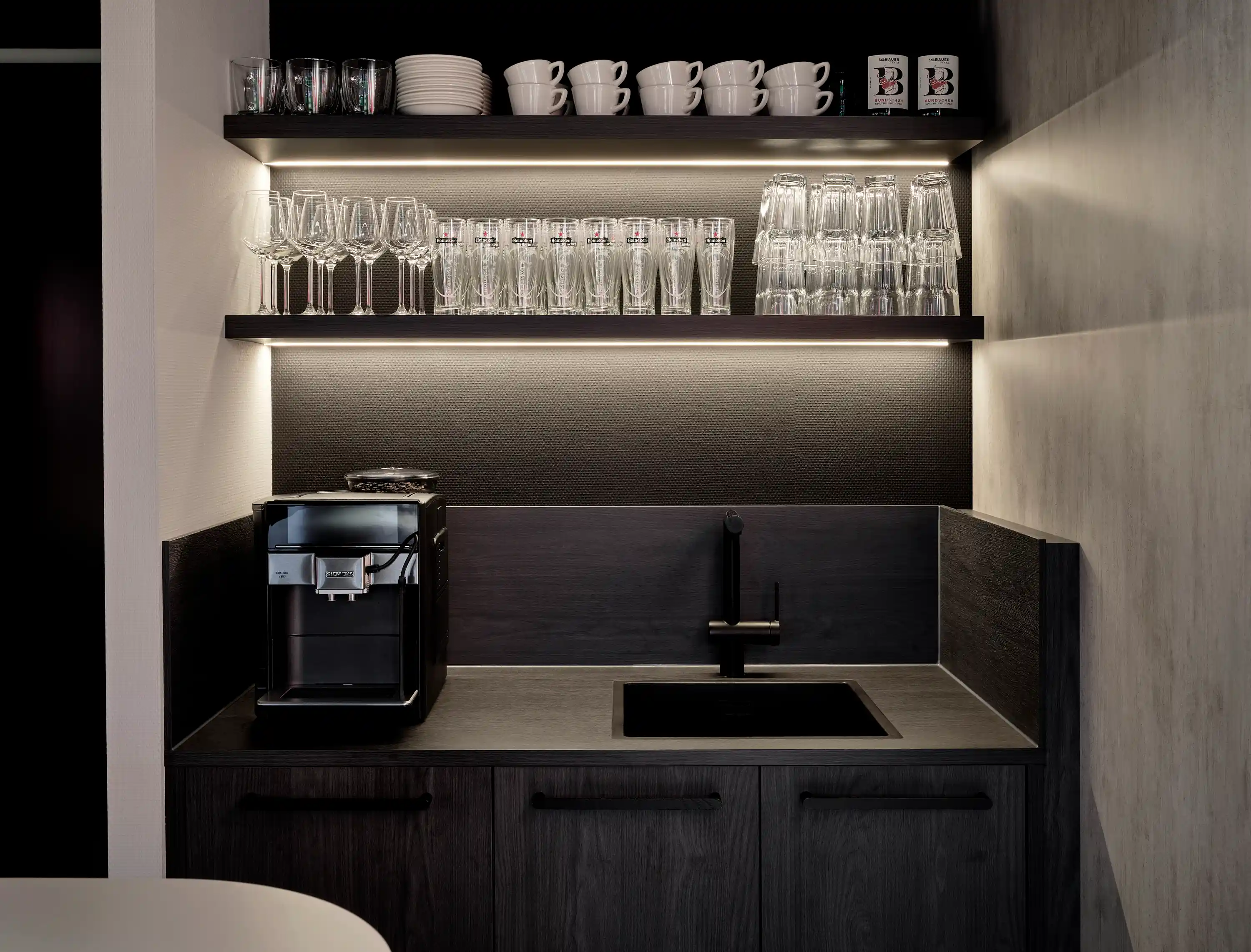
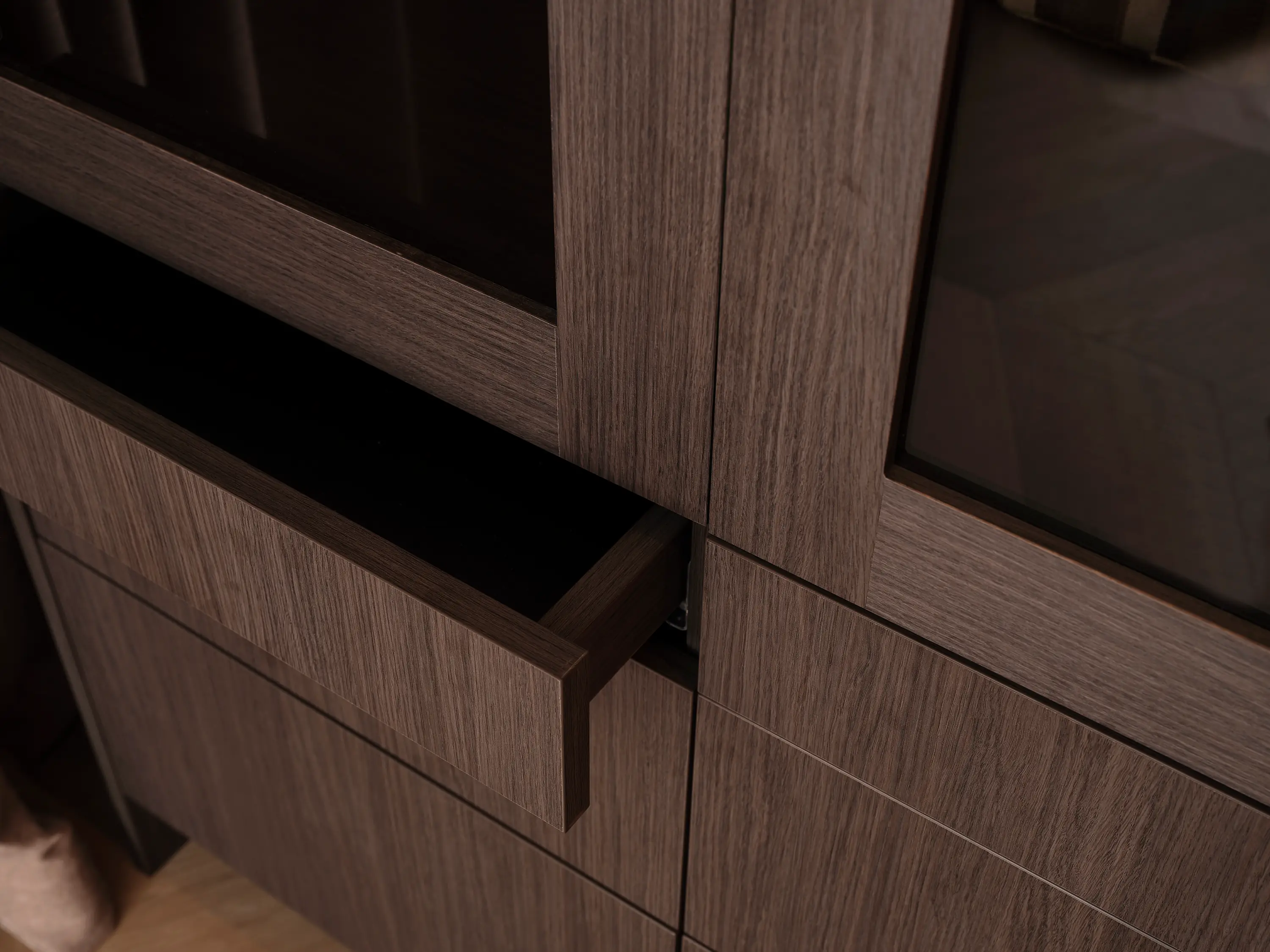
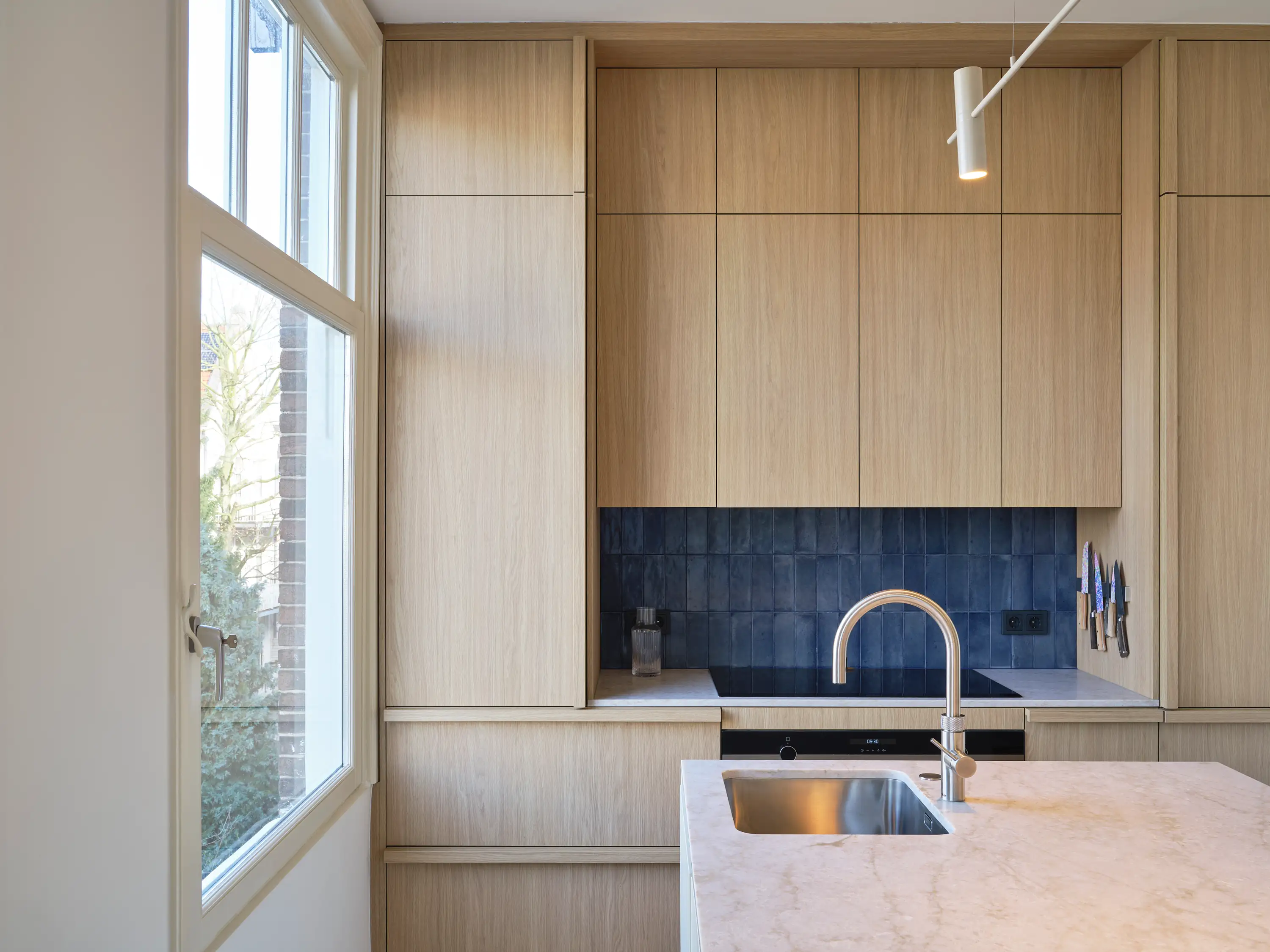
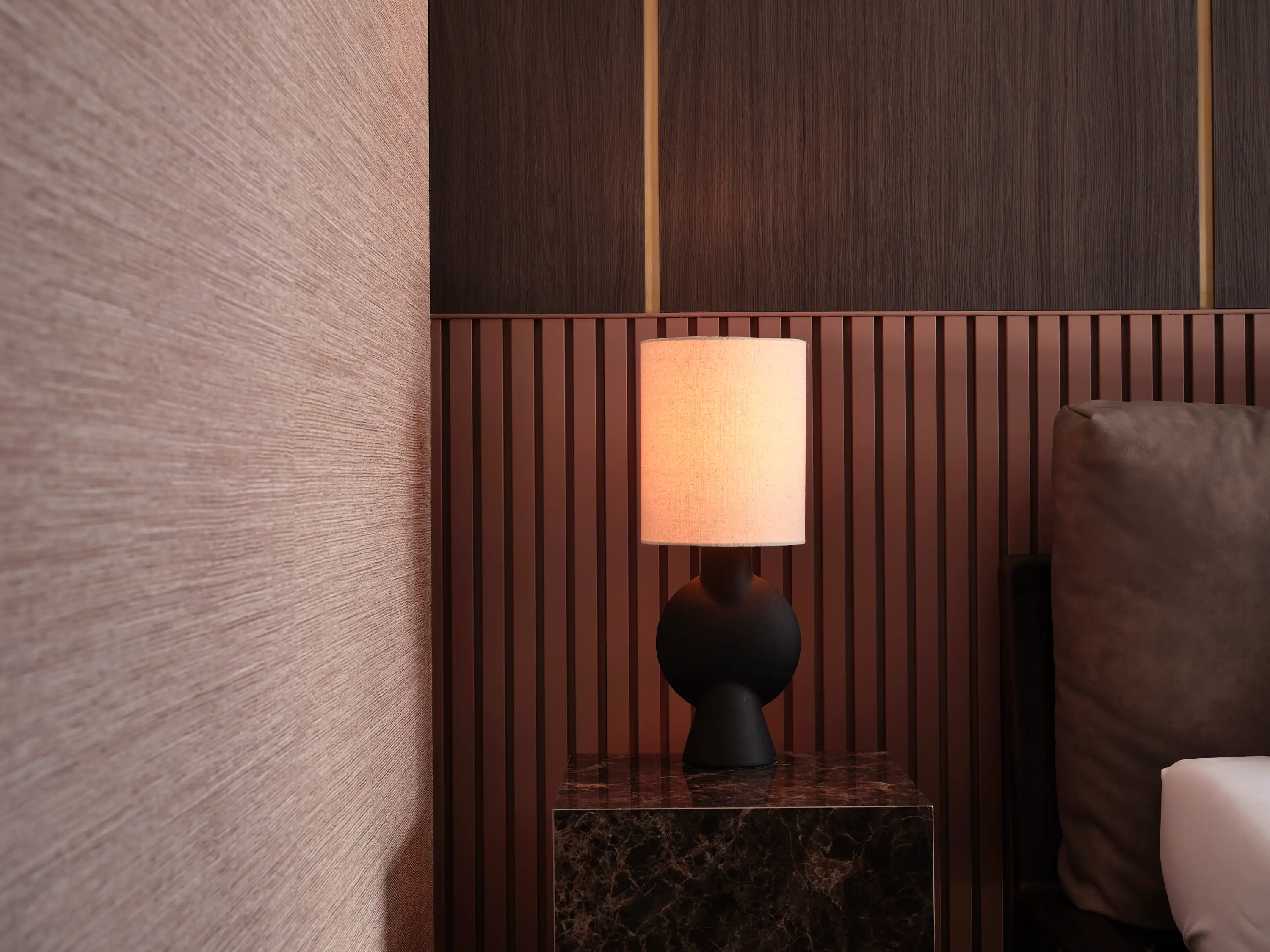
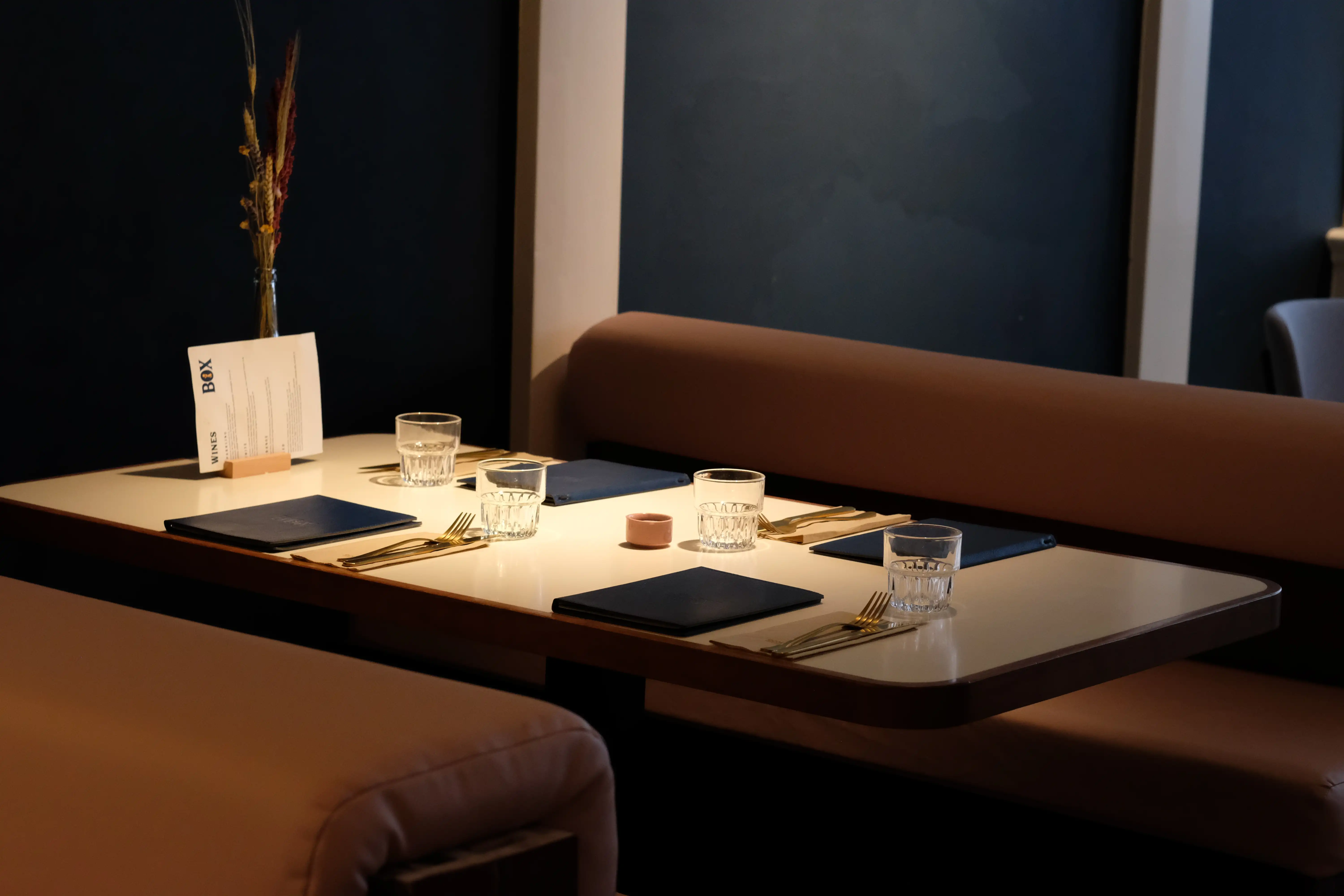
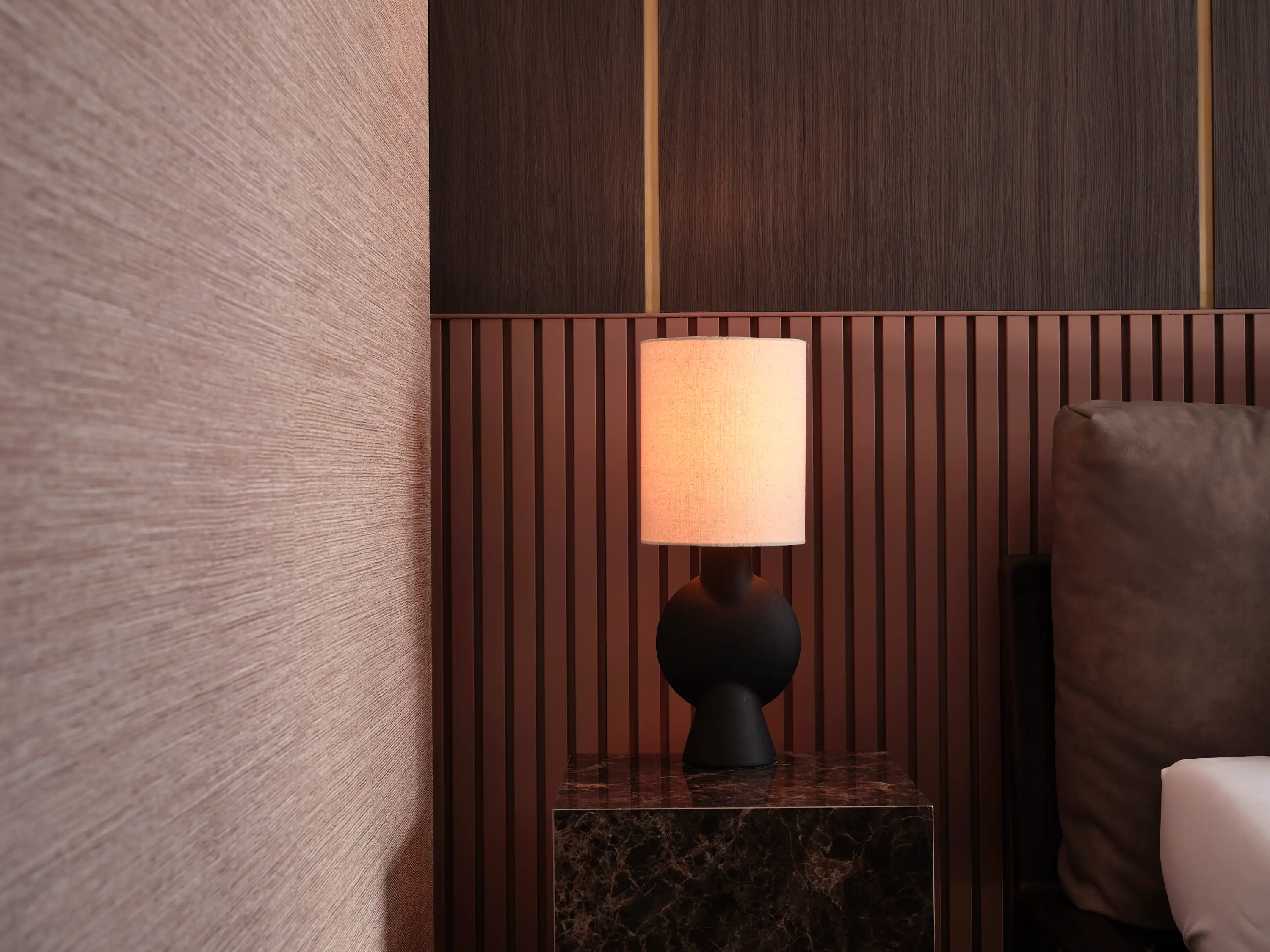